REGISTRO DOI: 10.5281/zenodo.8025291
Murillo Balabenute Milani;
Marcos Vinicius Nunes da Silva;
Vinicius Peixoto Vendramini;
Orientador: Josemar dos Santos.
RESUMO
Os motores automotivos são algumas das peças mais debatidas nos últimos anos, além de integrarem uma lista de principais componentes de uma das maiores indústrias do mundo. Por conta disso, o entendimento sobre motores como os de ciclo de otto se mostram importantes para que se estabeleça novos padrões de qualidade e novos sistemas complementares, como o sistema de injeção direta. Pensando nisso, o presente trabalho apresenta como objetivo geral registrar a evolução da tecnologia voltada para a parte de injetores de combustíveis em motores de ciclo de Otto, levando ao bico de injeção direta que, por sua vez, cada vez mais avança no sentido da sustentabilidade. Além disso, como objetivos específicos: apresentar o ciclo de otto e suas funcionalidades; discorrer sobre os injetores de combustíveis; apresentar o panorama geral da influência dos motores nos quesitos de sustentabilidade. Para alcançar tais objetivos, utiliza-se de revisão bibliográfica como método de pesquisa.
Palavras-chave: Ciclo de Otto; Injeção direta.
ABSTRACT
Automotive engines are some of the most debated parts in recent years, in addition to being part of a list of main components of one of the largest industries in the world. Because of this, the understanding of engines such as the Otto cycle is important to establish new quality standards and new complementary systems, such as the direct injection system. With that in mind, the present work has the general objective of registering the evolution of technology focused on the part of fuel injectors in Otto cycle engines, leading to the direct injection nozzle which, in turn, increasingly advances towards sustainability. In addition, as specific objectives: to present the otto cycle and its functionalities; talk about fuel injectors; present an overview of the influence of engines on sustainability issues. To achieve these objectives, a bibliographic review is used as a research method.
Keywords: Otto cycle; Direct injection.
1. Introdução
Em 1908, Henry Ford criou o primeiro Ford T, o motor de 4 tempos ciclo otto, que é usado até os dias de hoje. Este motor está em constante atualização, inclusive seus sistemas e subdivisões. Estes ciclos estão ligados a cada década e a cada tecnologia disponível no mercado e são muito conhecidos pelo gasto energético obtido. A partir da evolução das tecnologias voltadas para esse sistema, estuda-se todos os seus componentes e suas devidas evoluções. O sistema de injeção é uma parte importante que com o passar dos anos foi sendo atualizada para se adequar às leis sancionadas pelos países para redução da emissão de gases poluentes e para se adequar a procura por combustíveis e por veículos mais eficientes e potentes.
Atualmente este sistema está atrelado a um conceito de downsizing, estes são motores de pequeno porte atrelados a um sobre alimentador, comum entre eles: o turbocompressor, essa tecnologia ajuda a diminuir o volume do motor, mantendo ou aumentando a potência do motor. A criação de um motor que trabalhe em conjunto com todas essas tecnologias, atrelados a um sistema de injeção extremamente eficiente, um combustível com alto poder calorífico e sustentável, contribuem com o avanço em relação aos comprimentos de normas e leis implantadas por meio de agentes regulamentadores.
Após a crise do petróleo na década 70, Brasil precisou recorrer a uma fonte de energia alternativa, já que o preço do barril de petróleo estava altíssimo, por conta do embargo feito pela Arábia Saudita, sendo assim a utilização deste combustível passou a ser incentivada no país por meio do programa PROALCOOL (OHASHI, 2008). A utilização de um combustível que contribua com a melhor relação de componentes entre o sistema é fundamental para o sucesso, sendo o etanol, um grande aliado para esse sucesso, pois se trata de um combustível com alta octanagem, permitindo que o motor atue ou trabalhe de forma mais eficiente.
Com a queda do petróleo no cenário global, o etanol aumentou de preço, perdendo assim mercado. Em 1989, houve uma crise no Brasil em 1989, devido à falta do etanol, consequentemente houve o fim do programa. Já 1993, sancionou-se uma lei no Brasil, para que 22% de etanol fosse adicionado a gasolina, com o objetivo de reduzir as emissões de gases poluentes. Atualmente o etanol está presente em 27% na gasolina do território brasileiro. O etanol possui alta eficiência e é considerado como um combustível mais “limpo”, portanto este estudo procurou analisar seus usos, características e benefícios para a sociedade brasileira, quais foram os impactos e os benefícios da introdução do sistema de injeção direta na frota veicular e qual a relação entre o uso do combustível etanol e do sistema de injeção direta.
1. 1. Justificativa
Desde o século XX os veículos vêm sendo utilizados muito frequentemente na vida cotidiana. Os veículos passaram ao longo de sua trajetória por algumas mudanças significativas no que tange à sua qualidade, tecnologia e eficiência. Sua mudança teve impacto principalmente sobre o sistema de injeção de combustível, que é um sistema essencial de todos os veículos. Atualmente, as leis decretadas acerca da poluição e a procura por veículos de maior autonomia trouxeram uma discussão sobre o sistema de injeção de combustível direta.
Os veículos mais antigos ainda são a maioria em circulação no território brasileiro, por mais que já pensassem na autonomia e na eficiência, o modo que esses veículos foram projetados e montados não traziam um bom desempenho para eles. Com a chegada da injeção direta de combustível correlacionado com turbo alimentação e a entrada de combustíveis renováveis para o abastecimento veicular, foi possível ter uma saída melhorada por trazer consigo uma grande economia, grande eficiência energética e diminuição na poluição e desgaste ambiental. Analisando dois motores, um com injeção indireta convencional e outro com injeção direta de combustível turbo alimentado, foi possível notar as diferenças e as particularidades de cada um.
1.2. Objetivos
Para cumprir o objetivo geral de compreender os usos do sistema de injeção direta de combustível em motores de ciclo otto, foram definidos os 5 objetivos específicos descritos a seguir:
Objetivo específico 1.2.1. Estudar os componentes do sistema direto de combustíveis
Objetivo específico 1.2.2. Levantar as evoluções obtidas nos últimos anos
Objetivo específico 1.2.3. Analisar e comparar os motores de diferentes tipos e sua eficiência
Objetivo específico 1.2.4. Entender qual a contribuição do sistema de injeção direta
Objetivo específico 1.2.5. Levantar quais são as contribuições do sistema para o desenvolvimento sustentável do planeta e para a ecologia
2. Revisão bibliográfica
2. 1. CICLO OTTO
O ciclo Otto é um ciclo termodinâmico idealizado que transcreve a operação de um típico motor a pistão de centelha. É o ciclo termodinâmico mais comum em máquinas, veículos e operam em quatro estágios: admissão, compressão, combustão e escape.
Figura 1 – Ciclo Otto
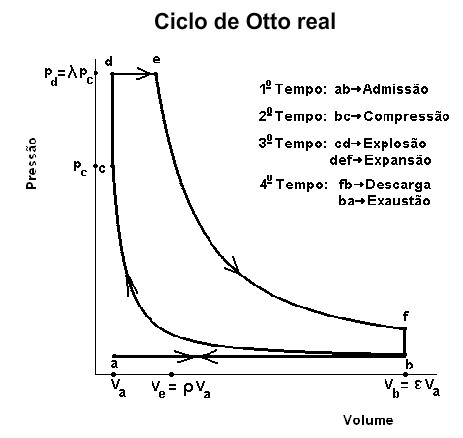
Fonte: LANG (2009).
As fases do ciclo são identificadas como:
0 1 – Admissão adiabática: ar é introduzido para o cilindro a pressão constante.
1 2 – Compressão isentrópica: ar no interior do cilindro é comprimido quando o pistão deslocado ponto morto inferior, PMI, para o ponto morto superior, PMS.
2 3 – Adição de calor a volume constante: calor é fornecido ao ciclo por meio da combustão. 3 4 – Expansão isentrópica: deslocando o pistão de PMS para o PMI produzindo trabalho.
4 1 – Exaustão a volume constante: o calor não aproveitado é rejeitado para a fonte fria.
1 0 – Exaustão a pressão constante: os gases resultantes da queima são expulsos com o deslocamento do pistão do PMI para o PMS.
-Primeira Vez (A) – Admissão: O pistão se move de PMS para PMI a válvula de entrada está aberta e a válvula de saída está fechada. Este movimento o pistão aumenta a capacidade dentro do cilindro, causando uma queda de pressão, a desigualdade de compressão criada entre o conjunto de admissão e o cilindro causa ar ou uma mistura ar-combustível é aspirado para dentro dos cilindros. O processo de formação da mistura de combustível é realizado por injetores elétricos, que podem ser colocados no trato de admissão (injeção indireta) e no cilindro (injeção direta).
-Segunda passagem (B) – Pressão: Quando atingindo o PMI, o processo de prensagem a válvula de admissão diminui pequenos graus após o PMI, sendo aproveitada a inércia do fluxo de entrada de ar aumentando o volume de enchimento cilindro, após fechar a válvula de admissão, o pistão atinge o ponto máximo a válvula está fechada. O composto é comprimido, o que causa um acúmulo na pressão e na temperatura dentro do cilindro.
-Ignição (C): próximo ao final da compressão, fornecendo a vela de ignição contato e a combustão começa. A máxima eficiência de combustão de um motor diesel a gasolina é atingida quando o avanço de ignição é normalmente ajustado para o valor entre 10° e 0° graus antes do ponto morto superior, APMS (BAÊTA, 2006).
-Estágio III (D) – Combustão e Expansão: A queima ocorre no período durante o qual o pistão se aproxima do PMS é curto. Ele começa a se aproximar à compressão termina, e quando o recuo começa. Mudanças intermitentes a mistura ar-combustível tem efeito na composição dos produtos de queima e melhora a temperatura e a pressão do fluido no cilindro. Cerca de 10 graus atrás do ponto morto superior, DPMS, a combustão ocorreu na metade do caminho para quase completa. DPMS de 30 a 40 graus, DPMS (HEYWOOD, 1988).
-A válvula fecha e expele a alta compressão de combustão os pistões PMI geram ação da motocicleta, reduzem a compressão e a temperatura do cilindro antes do pistão chegar o PMI. Abra a válvula de transferência ou válvula de sangria (E) antecipadamente: a expansão ocorre, a válvula de exaustão se abre e a exaustão começa. Temperatura a pressão do fluido no cilindro permanece alta em relação à barra de combustível. Escape, ou seja, a diferença de pressão entre a parte interna do cilindro e esta última o sistema de escape mantém os gases de escape fora dos cilindros à medida que o pistão se aproxima do PMI, a ação de bombeamento é reduzida. Os gases de escape sempre têm uma entalpia alta, o que reduz a eficiência do ciclo térmico (BAÊTA, 2006).
-Quarta passagem (F): Quando o pistão atinge o PMI, o cilindro ainda contém gás devido à combustão na pressão dos dutos de escape. Quando a porta de exaustão permanece aberta e o pistão se move de PMI para TDC, a maioria dos gases de escape restantes são expelidos, deixando apenas o volume da câmara de combustão ocupado por esses gases quando acabar, as válvulas de admissão começam a se abrir e as válvulas de escape se fecham. Esse é chamado o momento em que ambas as válvulas se abrem simultaneamente, o cruzamento ou sobreposição das válvulas facilita a troca do gás residual queime com mistura fresca. Ao final da exaustão, o ciclo recomeça (PULKRABEK, 1997).
Figura 2 – Ciclos do Motor
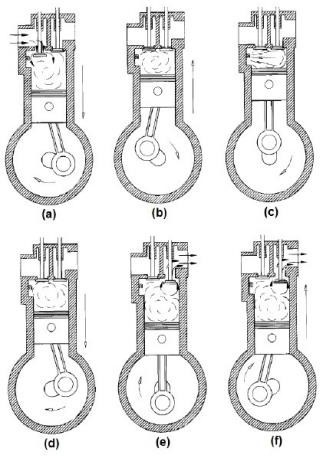
Fonte: PULKRABEK (1997).
2.2. RELAÇÃO ENTRE COMPRESSÃO E O NÚMERO DE OCTANOS
A compressão em motores ciclo Otto e o número de octanas é uma questão importante em engenharia automotiva. Basicamente, o número de octanas é uma medida da capacidade de um combustível resistir à detonação ou auto-ignição em um motor. Quanto maior o número de octanas, mais resistente o combustível é à detonação. A compressão nesse motor é a relação entre o volume total do cilindro quando o pistão está em seu ponto mais baixo e o volume total quando o pistão está em seu ponto mais alto. Quanto maior a compressão, maior a pressão e a temperatura no cilindro durante a combustão. Em sua maioria, motores com maior compressão requerem combustíveis com maior número de octanas para evitar a queima precoce. Isso ocorre porque a alta pressão e temperatura no cilindro durante a combustão é responsável pela reação química.
Geralmente, os motores com níveis de mais altos atendem padrões com números de octanagem mais altos para evitar a detonação precoce. Isso porque a alta pressão e temperatura no cilindro podem fazer com que o combustível entre em combustão antes do momento ideal para a combustão da vela. Se isso ocorrer, o motor pode ser danificado ou falhar. No entanto, motores com menor compressão podem utilizar combustíveis com menor número de octanas sem problemas. Essa relação entre compressão e número de octanas é importante para garantir o desempenho e durabilidade do motor, sendo assim, temos outros benefícios que incluem eficiência de combustível e a redução das emissões. A razão entre o volume e a massa é apreciada pela aprovação:
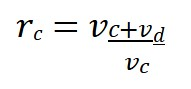
Onde é o volume da câmara de combustão [m³] e vd é o volume deslocado [m³]. A relação (ou taxa) de compressão é a relação entre o volume inicial e o volume final. A relação de compressão da gasolina é 6:1 a 8:1; do álcool é 12:1 a 14:1 e do óleo diesel é de 16:1 a 18:1 (Apostila de motores de combustão interna UFPEL).
Figura 3 – Relação entre a compressão do pistão
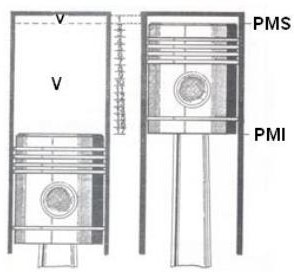
Fonte: UNIVERSIDADE FEDERAL DE PELOTAS (2013).
2.3. EFICIÊNCIA VOLUMÉTRICA EM MOTORES DE CICLO OTTO
Os componentes de um sistema de admissão de ar do motor incluem filtros de ar, trocadores de calor, corpos de aceleração, coletores, vigias e válvulas que limitam a quantidade de ar que um motor de um determinado deslocamento pode aspirar. O parâmetro usado para medir a ordem do processo de admissão do motor é chamado de eficiência volumétrica (HEYWOOD, 1988).
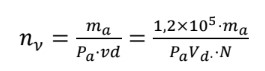
No caso da injeção direta, o combustível é injetado de forma que não bata na parede do cilindro, então todo o calor de vaporização do combustível é utilizado para resfriar o ar, mas no caso da injeção indireta, esse calor é transmitido diretamente para o cilindro. Paredes ou válvulas do coletor de admissão. Os veículos que usam injeção direta são, portanto, mais eficientes volumetricamente. Mudar o sistema de injeção de combustível de injeção indireta para injeção direta pode melhorar a eficiência volumétrica em até 9% sob condições estequiométricas de gasolina (WYSZYNSKI et al., 2002).
Algumas variáveis que são importantes sobre eficiência volumétrica são:
- Tipo de combustível
- Temperatura da mistura
- Maximização da troca de calor em relação ao ar/combustível
- Relação entre admissão e escape
- Volume de compressão
- Rotação do motor
- Tamanhos de dutos de admissão e escape
- Tamanhos de válvulas e comandos
E quanto maior essa capacidade, maior a massa mistura, então a eficiência volumétrica do motor é maior. Determinando quanto adicionar à mistura a quantidade de gás queimado no cilindro e lá permanecendo, bem como a alteração desses parâmetros pode afetar a eficiência volumétrica. A mistura flui ao longo dos coletores de admissão e escape. Nestes casos, um gradiente de pressão de fluxo reverso é gerado. A determinação de válvulas por efeito de inércia faz avançar e retardar a abertura da válvula (efeito ram) e dimensionar componentes da mistura que afetam a eficiência volumétrica (FILHO, 2014).
2.4. EFICIÊNCIA TÉRMICA
Denomina-se eficiência térmica, a razão entre a potência e o calor que são gerados pela combustão. A equação referente a esta razão é definida por:
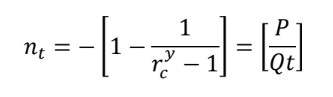
Portanto, pode-se dizer que a razão volumétrica de compressão e o calor específico, aumenta a eficiência térmica (GIACOSA, 1988).
Figura 4 – Relação entre eficiência térmica e compressão
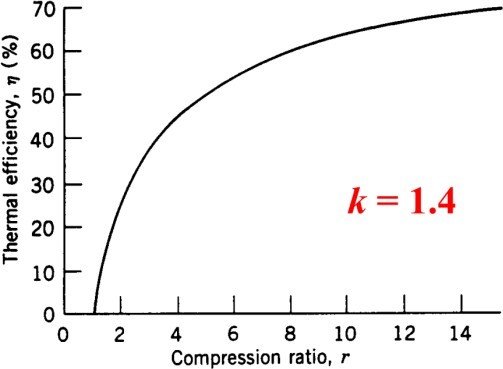
Fonte: UNICAMP (2017).
2.5. EFICIÊNCIA DA QUEIMA DE COMBUSTÍVEL
O tempo disponível para o processo de combustão no motor é tão curto que não há tempo para que todas as moléculas de combustível queimem. Ele reage quimicamente com moléculas de oxigênio. A temperatura fria perto ou nas paredes do cilindro combinada com a expansão pode extinguir a chama antes que todo o combustível seja consumido. Como resultado, uma pequena porção do combustível não reage e é expelida com o escapamento. A eficiência da combustão é uma consideração da porcentagem de combustível queimado. Quando o motor está funcionando normalmente, os valores típicos de eficiência de combustão ficam na faixa de 95 a 98% (PULKRABEK, 1997).
2.6. CONVERSÃO DE COMBUSTÃO
Definida pelo trabalho realizado e a quantidade de energia fornecida pelo combustível. Essa relação pode ser estabelecida como produto da massa pelo poder calorífico, PCI, este inferior ao combustível define o seu conteúdo energético. A taxa de consumo de combustível pode ser definida como a razão entre a massa de combustível e a potência, indicando assim, a eficiência do combustível para o trabalho do motor ao gerar eletricidade (HEYWOOD, 1988).
2.7. POTÊNCIA DO MOTOR
Para atender a norma NBR1585 da ABNT (1996), os motores com condições atmosféricas diferentes da definida na norma, precisam ser corrigidos, para os valores de referência.
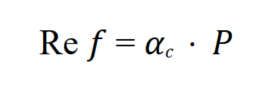
Em que, Re “f” é o valor da potência do motor nas condições de referência em [km] e “ac” seria o fator de conversão.
Obtém-se a equação do fator de correção:
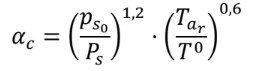
Em que, “ps” pressão ambiente [Kpa], “Tar” temperatura do ar admitido pelo motor [°c], “ps” e “to” , pressão de referência das mesmas unidades.
A pressão seca (Os) é determinada pela norma NBR 5484 (1985):
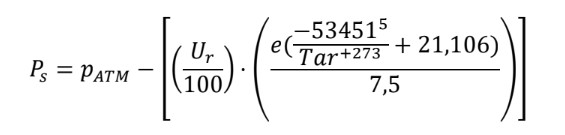
Na qual, “pATM” pressão atmosférica [Kpa] e “Ur” unidade relativa do ar [%].
A norma NBR 1585 da ABNT (1996), não faz distinção entre motores aspirados ou turboalimentados. Em casos de sobre alimentação através de compressores têm-se válvulas como válvula Wastegate que controla essa pressão. Por ser controlado por uma válvula externa, não é possível aplicar o fator de correção em motores turboalimentados, pois a sobre alimentação máxima de pressão não varia em função da altitude. No entanto, a temperatura atmosférica também influencia no resultado, sendo assim, deveria ser corrigida em motores turboalimentado (BAÊTA, 2006).
2.8. SISTEMA PISTÃO BIELA MANIVELA
Figura 5 – Sistema Pistão Biela Manivela
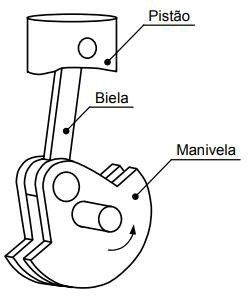
Fonte: MAIA; MATOS; JÚNIOR (2021).
Este mecanismo é comumente utilizado em sistemas mecânicos para transformar movimento de rotação em movimento de translação, sua principal aplicação seria motores de combustão interna. A velocidade média do pistão é o padrão mais apropriado que a velocidade do rotacional do virabrequim para se obter uma correlação com o comportamento do motor. As velocidades de fluxo dos gases no sistema de admissão e no cilindro, por exemplo, são obtidas em escala com a velocidade média do pistão (HEYWOOD, 1988).
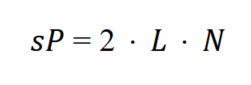
Já a capacidade de realização de trabalho gerada por um motor provém do torque, uma medida relativa ao desempenho do motor obtida pela razão do trabalho produzido por ciclo pelo volume deslocado por ciclo, é a pressão média efetiva ou PME (HEYWOOD, 1988). O PME é muito útil, pois considera o curso do tamanho do motor, tornando possível a comparação do desempenho, sendo eles de diferentes tamanhos (FERGUSON, 2015). A PME é a pressão média exercida no pistão na fase de expansão, gerando o torque médio. Dividindose a pressão máxima do ciclo pela pressão média efetiva indicada ou PMEI obtém-se um parâmetro da qualidade da pressão ao longo de todo o ciclo (BAÊTA, 2006). O aumento da pressão dentro do coletor de admissão é diretamente proporcional ao PME (GANESAN, 1995).
A equação que demonstra essa ação é:
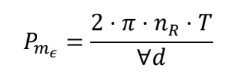
Onde T é o torque produzido no virabrequim [N.m]. Uma parte da potência produzida pelo cilindro é utilizada para admitir mistura e liberar gases provenientes da combustão. Outra parte da potência gerada pelo motor é utilizada para quebrar o atrito dos rolamentos, pistões, entre outros componentes mecânicos do motor, sendo assim, todas essas requisições são chamadas potência de atrito (HEYWOOD, 1988). A diferença entre a PMEI e PME é conhecida como pressão de atrito ou simplesmente pressão média motorizada, “Pmm” (BAÊTA, 2006).
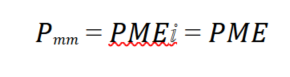
No entanto, há alguns outros métodos para o cálculo da pressão de atrito, sendo eles:
- Método de corte: Este método, corta a alimentação de combustível de um dos cilindros eentão o pistão passa a ser deslocado pelos demais. A perda de atrito é determinada neste caso pela diferença entre potência antes e depois do corte de combustível.
- Método motorizado: Neste método o motor sem alimentação é tracionado por outro. Apotência motorizada requerida para movimentar o motor é considerada como a perda causada por atrito (BAÊTA, 2006).
Figura 6 – Relação entre pistão Biela (cálculos)
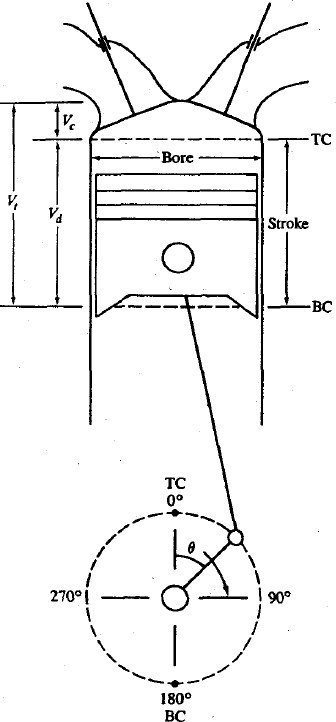
Fonte: HEYWOOD (1988).
O PME e PMEI determinam a razão da eficiência mecânica. A partir da comparação entre esses pontos fica evidente que baixas cargas geram menor eficiência mecânica, pois este utiliza a maior parte desta carga com o atrito. No entanto, conforme a carga aumenta, a eficiência mecânica aumenta também. Ao aumento da carga aplicada ao motor, a potência indicada aumenta em uma proporção maior do que a potência de atrito, resultando em uma redução no consumo específico de combustível (BAÊTA, 2006). Em condições de marcha lenta, a carga aplicada é controlada pelo corpo de borboletas, diminuindo assim a eficiência mecânica levando a zero em condições de marcha lenta do motor (HEYWOOD, 1988).
2.9. COMBUSTÃO
Nos motores comuns a ignição é feita através do contato de uma pequena parte da mistura de combustível com a vela de ignição cuja temperatura varia de 3000° a 6000°C, sendo disseminada através da câmara de combustão de maneira progressiva e com uma velocidade controlada (BAÊTA, 2006; FILHO, 2014). Como este processo tem um tempo determinado, ele é iniciado antes do PMS, próximo ao final da compressão. No entanto, caso esse processo ocorra antes do tempo determinado, este acaba por gerar um grande aumento de pressão e de temperatura devido ao trabalho excessivo de compressão. Para o processo que foi ocorrido depois do tempo determinado, o aumento de pressão será tardio, reduzindo seu trabalho e enviando calor à exaustão, podendo assim danificar algum componente do motor (BAÊTA, 2006).
Existem dois fatores muito importantes para que se determine a velocidade de frente de chama. Um fator muito importante para a uma combustão eficiente é a taxa de reação. A taxa de reação é um processo químico, na qual, a chama se mistura com o combustível e com o ar que não foram queimados durante sua propagação e a taxa de transposição ocorre devido ao movimento da frente de chama relativo às paredes do cilindro e resultado da diferença de pressão estabelecida entre os gases queimados e não queimados na câmara de combustão (GANESAN, 1995).
Conforme Ozdor, Dulger e Sher (1994), este processo pode ser dividido em 4 etapas:
- centelha e início da chama,
- desenvolvimento inicial do Kernel,
- propagação da chama turbulenta, sendo esse o principal estágio da combustão,
- término da chama.
A primeira fase inicia-se por conta do aumento de tensão entre os eletrodos da vela de ignição, decorrente de uma carga elétrica. O tamanho do Kernel, pode variar de acordo com as configurações da vela e da energia depositada, essas por sua vez, podem ser causadas por oscilações na densidade da mistura ar-combustível, tensões viscosas da mistura ar combustível ou pela velocidade do fluxo perto da vela de ignição (OZDOR; DULGER; SHER, 1994).
Na fase de arco, o kernel, está crescendo em tamanho e sendo esfriado a quase 6000K por conta da expansão e da transferência de calor para os eletrodos. Por sua vez a última fase desta etapa é a descarga brilhante ou glow discharge, sua característica varia de acordo com o sistema de ignição utilizado, sendo caracterizada por uma tensão relativamente baixa 10w, no entanto, seu tempo de duração é maior que o tempo de energia total liberada, equivale a 90% da energia total liberada pela vela de ignição (HEYWOOD, 1988; OZDOR; DULGER; SHER, 1994).
Para o segundo estágio, deve-se assumir que ocorre quando a massa de combustível queimada atinge cerca de 1 a 2%, neste momento é iniciada a chama no espaço entre a vela e a esfera. Sendo assim, nesta fase de combustão são atribuídas flutuações na concentração da mistura ar-combustível, diluição por gases residuais de escape e predominantemente por condições termodinâmicas próximo à vela de ignição (OZDOR; DULGER; SHER, 1994).
No terceiro estágio, esta mistura é na sua maior parte queimada, sendo ela 10 a 90% de sua fração massa de combustível, nesta fase a iniciação ocorre com a propagação da chama e terminando ao ser totalmente consumida para frente de chama. Por conta deste se iniciar no centro do Kernel, alguns fatores como localização da vela de ignição e as configurações da câmara de combustão influenciam a área instantânea de propagação da frente de chama. Direcionado pelo cilindro, o fluxo médio distorce a propagação esférica da frente de chama, fazendo com que o centro do Kernel seja deslocado a sua área original, no entanto, quanto maior a taxa da queima, menor a distorção da frente de chama e menor ainda o deslocamento do centro do kernel (OZDOR; DULGER; SHER, 1994).
A decomposição da massa de combustão é limitada a 30°C, representando o ponto de máxima eficiência de conversão de combustível. Assim, a duração da combustão em que 10% a 90% da massa queimada é queimada determina a eficiência de conversão de combustível para qualquer duração de combustão, resultando em ganhos de eficiência de conversão de combustível reduzidos por meio de efeitos termodinâmicos, trabalho de bombeamento reduzido ou perdas de transferência de calor reduzidas (AYALA; et al., 2006). No quarto e último estágio, há a extinção da frente de chama ao colidir com as paredes do cilindro, perdendo assim calor e se extinguindo. Neste caso, ainda pode haver combustíveis sem queima, sendo assim o mesmo ao se chocar com a parede pode vir a queimar.
.10. AVANÇO IGNIÇÃO
Este processo é focado no tempo necessário para a queima completa do combustível, gerando uma produção de trabalho aproveitada pelo pistão durante a fase de expansão.
Figura 7 – Avanço de Ignição
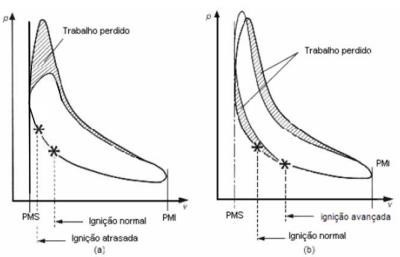
Fonte: BAÊTA (2006).
Para cada condição ideal de funcionamento do motor, é fornecido um valor máximo de torque conhecido como torque máximo de frenagem ou MBT, que depende do desenvolvimento e propagação da frente de chama, do comprimento da câmara de combustão e de como são extintos. Determine o valor do avanço de ignição em MBT se 50% da fração de massa de combustão ocorre em torno de 8 a 10° CA e o pico de pressão ocorre em torno de 13 a 15° CA (HEYWOOD, 1988).
2.11. COMBUSTÍVEL
A fim do devido funcionamento, o combustível é um dos principais pontos geradores, para que o motor possa trabalhar, sendo que suas propriedades têm uma significativa influência na eficiência de conversão do combustível. Combustíveis fósseis derivados do petróleo como gasolina e diesel, são comumente utilizados em veículos. Existem também alguns combustíveis que são alternativos, renováveis e biodegradáveis como o etanol, metanol, gás natural, hidrogênio verde e biodiesel, atualmente são os combustíveis mais utilizados, devido à necessidade de desenvolvimento sustentável e também pelas legislações impostas pelo poder público. Cada combustível tem suas propriedades físico-químicas e esses combustíveis foram escolhidos pelas suas características. No caso, o etanol, por se tratar de um combustível renovável e sustentável e de ótimo custo-benefício, é usado frequentemente no Brasil.
2.12 ETANOL
O etanol é o principal composto orgânico do grupo dos álcoois, por isso é comumente chamado simplesmente de álcool. Sua fórmula está representada abaixo na figura 8:
Figura 8 – Fórmula do Etanol
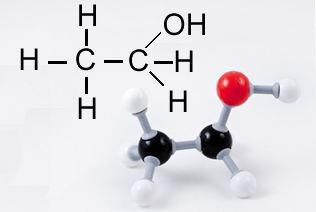
Fonte: FOGAÇA (2014).
Ele é obtido principalmente por meio da fermentação de açúcares e cereais (por isso, é chamado muitas vezes de “álcool de cereais”). No Brasil, o etanol é produzido somente pela fermentação da cana-de-açúcar, e nos Estados Unidos, o milho transgênico é muito utilizado, mas também usam beterraba, arroz, cevada e batata. É estimado que cerca de 1 tonelada de cana produz 70 litros de etanol, o processo de fabricação de etanol é muito mais rentável quando a cana-de-açúcar é usada como matéria prima. O processo de produção passa pelas seguintes etapas:
- Trituração e moagem da cana para a obtenção da garapa com alto teor de sacarose;
- Concentração e cristalização da garapa para a produção de duas porções: açúcar escuro, que é usado para produzir o açúcar comum, e o melaço, que é usado para se produzir o álcool;
- Fermentação do melaço obtendo-se o mosto fermentado, com cerca de 12% de etanol em volume;
- Destilação fracionada do mosto fermentado que produz o álcool comum a 96ºGL (96 graus Gay-Lussac), formando um composto de 96% de etanol e 4% de água.
No Brasil, a produção de cana-de-açúcar e a maioria das usinas produtoras de etanol se concentram nas regiões Centro-Sul e Nordeste. Além desse método, pode-se também fabricar o etanol por meio da reação de adição de água ao eteno. Nacionalmente são produzidos e consumidos dois tipos diferentes de etanol combustível: o anidro e o hidratado. O etanol anidro (ou absoluto): é praticamente isento de água (quase 100% etanol), esse combustível é adicionado a gasolina. O etanol possui uma quantidade energética inferior à da gasolina, porém como sua relação ar/combustível também é menor e possui oxigênio em sua composição química, menos ar é necessário para a combustão completa. As misturas arcombustível de etanol têm maior energia utilizável para a mesma massa de ar (BAÊTA, 2006).
Segundo Pulkrabek (1997):
Fórmula química e molecular do etanol. O etanol é representado pela fórmula C2H6O, ou, de forma mais detalhada, CH3CH2OH. Isso significa que o composto é formado por dois átomos de carbono © ligados à cinco átomos de hidrogênio (H) e a um átomo de oxigênio (O) ligado a outro hidrogênio. A presença do grupo OH, chamado de hidroxila, em sua composição, faz com que o etanol se torne uma substância polar, ou seja, que possua polos eletrônicos distintos em sua cadeia, algo possível graças à presença do oxigênio. Por causa dessa característica, o álcool se mistura facilmente com a água e outros líquidos que também são polares (PULKRABEK, 1997).
Dentre os compostos químicos, o etanol pode ser considerado um composto orgânico. Os compostos orgânicos são aqueles formados por cadeias de carbono. Isso faz com que ele seja encontrado mais facilmente em estado líquido ou gasoso, ao contrário dos compostos inorgânicos, como os minerais, que em seu estado natural costumam ser sólidos. Entre os compostos orgânicos, o etanol faz parte da família dos álcoois, compostos em que o carbono saturado (com todas as ligações preenchidas) liga-se com a hidroxila.
Seu nome deve-se à junção do prefixo “etano”, comum a todos os compostos orgânicos com dois átomos de carbono em sua cadeia, com o sufixo “ol”, relativo aos álcoois que possuem apenas uma hidroxila em sua formação. Dessa forma, não é inteiramente correto chamar o etanol apenas de “álcool”, pois álcool é qualquer elemento orgânico que possui a hidroxila “OH” ligada a um carbono saturado (metanol, butanol e propanol). Dentre todos os álcoois, o etanol é o mais comum de ser obtido. A sua massa molecular é composta por 52,24% de Carbono, 13,13% de Hidrogênio e 34,73% de Oxigênio.
2.13. MASSA MOLECULAR E DENSIDADE
Por possuir poucos elementos químicos em sua formação, e cadeia com apenas dois átomos de carbono, o etanol é um composto orgânico muito leve, e o mais leve dos combustíveis comuns se comparado com a gasolina, que possui cadeias entre quatro e doze carbonos, e com o diesel, que possui mais de doze carbonos. Isso faz com que ele seja mais fácil de ser obtido e que teoricamente polua menos, fato que depende também da tecnologia empregada no motor dos veículos. A leveza do etanol também contribui para seu estado natural líquido e por possuir um baixo ponto de ebulição (78,4°C). Para calcular a massa molecular do etanol, assim como de qualquer composto químico, soma-se número de massa de cada um dos elementos de sua formação.
Possui fórmula molecular C2H6O, é somado duas vezes o número de massa do carbono (2 x 12), com seis vezes o número de massa do hidrogênio (6 x 1), mais o número de massa do oxigênio (15,99), chegando ao resultado de 46,07u (unidade de medida). Quando puro e com temperatura próximo dos 25°C, o etanol possui uma densidade de 789 g/cm³. Isso significa que a cada centímetro cúbico o etanol pesa apenas 0,789 gramas. Os valores mudam dependendo da mistura e da temperatura a qual ele está submetido, sendo que o álcool combustível possui densidade que varia de 0,82 a 0,88 g/cm³.
Assim, o etanol é um pouco mais denso do que a gasolina, cuja densidade varia entre 0,72 e 0,76 gramas por centímetro cúbico, porém ele é menos denso que a água, que possui densidade média de 1 g/cm³. A densidade dos compostos muda conforme a temperatura, pois essa variação influencia em seu volume. Ou seja, a mesma quantidade de material pode ocupar menos ou mais espaço em função da quantidade de calor. Isso ocorre às vezes em caminhões que carregam combustíveis, eles acabam sofrendo variações na quantidade de litros que estão carregando, embora a quantidade de matéria que eles transportam continue sendo a mesma.
2.14. PONTO DE EBULIÇÃO E SOLIDIFICAÇÃO
Em temperatura ambiente, o etanol será sempre encontrado no estado líquido, pois ele atinge seu ponto de ebulição quando submetido a uma temperatura de 78,4°C (se transformando em gás), e atinge seu ponto de solidificação a -114,3°C (se transformando em sólido) considerando a temperatura a 1 atm.
2.15. PONTO DE FULGOR E AUTOIGNIÇÃO
A partir da temperatura de 13°C, o etanol começa a emitir vapores que, em contato com outras fontes de calor, possibilita a sua combustão. Essa marca é chamada de ponto de fulgor, o que não significa que ele necessariamente pegue fogo nesse ponto, mas indica que há chances de isso acontecer caso haja um fator externo que predisponha a isso. Já o seu ponto de autoignição significa a temperatura mínima para que a combustão ocorra. No ponto de autoignição a combustão irá ocorrer mesmo sem a influência de nenhum fator externo, para o etano a temperatura de autoignição é de 363°C.
É por isso que, em baixas temperaturas, o álcool combustível não realiza a combustão dentro do motor, e consequentemente não atua como um combustível para a arrancada e deslocamento dos veículos. Abaixo dos 13° C, o etanol perde sua capacidade de combustão e se torna inutilizável como combustível. Pelo seu baixo ponto de fulgor, o álcool é considerado uma substância inflamável (ponto de fulgor menor que 70°C) e por isso que, quando armazenado, ele traz a letra “F” em sua embalagem, acompanhada pelo desenho de uma chama. Entre os combustíveis mais comuns, apenas a gasolina tem ponto de fulgor menor que o etanol, sendo o dela de – 40°C, enquanto o diesel e o biodiesel possuem pontos de, respectivamente, 62°C e 130°C.
2.16. PODER CALORÍFICO: POTENCIAL ENERGÉTICO
Poder calorífico é a quantidade de energia que um combustível é capaz de gerar em sua queima dentro do motor. Essa propriedade diz respeito à quantidade de energia interna que cada substância contém. Quanto maior o poder calorífico do combustível, maior é sua energia, e por isso, melhor o seu rendimento. O poder calorífico do etanol combustível comum (etanol hidratado) é de 5.380 quilocalorias por litro (kcal/l). Esse valor corresponde a aproximadamente 70% do poder calorífico da gasolina, calculado em 8.325 kcal/l. É por isso que, em média, o litro do etanol faz 70% da distância que o litro da gasolina percorre, pois, a energia contida em 1 litro da gasolina é 30% maior.
O combustível líquido de maior poder calorífico é o do diesel, que gera 9.160 quilocalorias por litro. O poder calorífico em massa da gasolina é superior ao diesel (11.230 contra 10.830), porém o litro deste rende mais devido à sua maior densidade (0,85 kg/l contra 0,72 kg/l). Um dos fatores para o menor poder calorífico do etanol é a pouca quantidade de hidrogênio (átomo com maior poder calorífico que existe) em sua cadeia e a presença do oxigênio (que tem baixo poder calorífico). Em geral, quanto maior a proporção de hidrogênio no combustível, maior é seu poder calorífico.
2.17. POTENCIAL HIDROGENIÔNICO (PH)
O PH é um índice numérico que varia entre 1 e 14 e mede o grau de acidez ou de basicidade de uma substância, o número 7 representa neutralidade, números menores que 7 são de soluções ácidas e números maiores que 7 determinam substâncias básicas. O PH do etanol, quando misturado em água, costuma variar entre 6 e 8, o que significa que a solução é praticamente neutra, ou seja, muito alcalina, nem muito ácida. Como a maioria das substâncias neutras, o etanol torna-se pouco agressivo ao ser humano, possuindo cheiro e consistência não prejudiciais, porém sua ingestão é definitivamente perigosa, podendo ocasionar desde mal-estar até coma e morte.
As vantagens do álcool como combustível são:
- Pode ser obtido de inúmeras fontes, tanto naturais quanto industrializadas;
- Contém alta taxa de octanagem e é altamente antidetonante. A maior resistência à batidapossibilita o uso de taxas de compressão maiores, resultando em um motor mais eficiente;
- Apresenta menores índices de emissões de poluentes quando comparado com a gasolina;
- Alto calor latente de vaporização, o que resulta em um maior resfriamento do processo deadmissão e compressão, aumentando assim, a eficiência volumétrica do motor;
- Baixo teor de enxofre no combustível.
Pode-se citar as desvantagens do álcool etílico, que conforme Pulkrabek (1997) são basicamente:
- Baixo conteúdo energético. Isso significa que quase duas vezes mais etanol são necessáriasem relação a gasolina para fornecer a mesma quantidade energética ao motor;
- A alta taxa de aldeídos nos gases de escapamento, que se configura como um problemaambiental;
- O álcool etílico é muito mais corrosivo que a gasolina a cobre, bronze, alumínio, borracha eplástico, impondo algumas restrições aos projetos de motores que utilizam esse combustível;
- Dificuldade de partida nos motores em temperaturas mais baixas, devido à baixa pressão devapor e vaporização.
Atualmente no Brasil, os sistemas de partida a frio são instalados nos veículos com motores que operam com etanol, porém, com uso da injeção direta eliminou-se esse problema no Brasil, pois mesmo em temperaturas de até -10°C, a partida do motor ainda é possível sem qualquer ajuda de sistemas auxiliares, como no caso do uso de combustíveis mais voláteis como gasolina ou sistemas de pré-aquecimento do combustível. Porém, para países de clima mais frio, isso ainda é um problema porque a gasolina é capaz de funcionar em temperaturas de até -40°C.
Figura 9 – Propriedades do Etanol
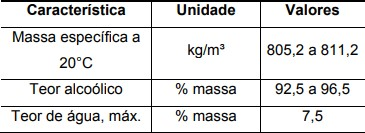
Fonte: AGÊNCIA NACIONAL DE PETRÓLEO (2015).
2.18. CARBURADOR
É possível considerar o carburador como um sistema de injeção, porque a admissão de combustível é feita atrás de um vácuo na câmera de combustão, que é um dos principais precursores do processo, já que administra mistura ar combustível nas devidas proporções para seu saudável funcionamento. Entretanto, com o avanço da tecnologia, que cada vez mais fazia com que os carros ficassem mais eficientes e mais potentes, o carburador que não cumpria com essas expectativas, porém o carburador, por diversas vezes causava uma interrupção no funcionamento do veículo, impossibilitando o deslocamento desse carro.
Figura 10 – Funcionamento Carburador
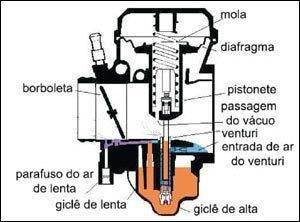
Fonte: MOTONLINE (2012)
2.19. INJEÇÃO ELETRÔNICA
A injeção eletrônica é um sistema utilizado em motores de veículos para controlar a quantidade de combustível e ar que é injetado no motor. Esse sistema é composto por um conjunto de sensores, atuadores e uma unidade de controle eletrônico (ECU). No Brasil esse sistema teve início em 1988, mais conhecido como LE jetronic, que fora desenvolvido pela Bosch e equipava o modelo Volkswagem Gol GTI, se tornando o primeiro veículo nacional a oferecer esta tecnologia.
Figura 11 – Primeiro Carro com Injeção Eletrônica
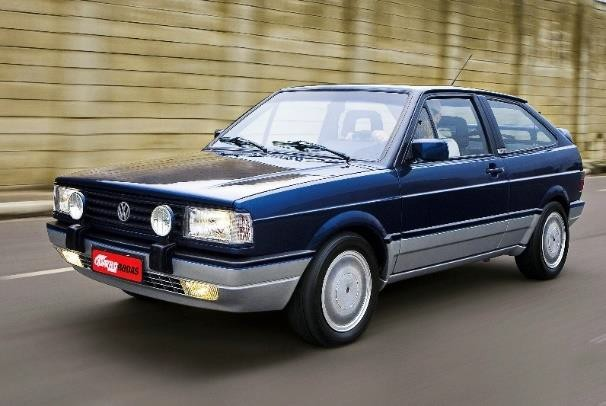
Fonte: BITU (2021)
Nesse sistema, sensores detectam as condições do motor, como a temperatura, a pressão do ar, a posição do acelerador e a taxa de rotação, e enviam essas informações para a ECU. Com base nessas informações, a ECU calcula a quantidade ideal de combustível que deve ser injetada no motor em tempo real. Os atuadores que são controlados pela ECU, são responsáveis por regular a pressão do combustível, a abertura dos bicos injetores e o tempo de abertura desses bicos. Dessa forma, o sistema garante que a quantidade de combustível que entra no motor seja a correta para que ocorra uma combustão completa e eficiente. A injeção eletrônica substituiu o sistema de carburador, que era utilizado anteriormente em motores de veículos.
Além de proporcionar um melhor desempenho do motor e uma economia de combustível, o sistema de injeção eletrônica também permite um controle mais preciso das emissões de poluentes, tornando os veículos mais sustentáveis. Existem diferentes tipos de injeção eletrônica, como a injeção direta, que injeta o combustível diretamente no cilindro do motor, e a injeção indireta, que injeta o combustível na entrada de ar do motor. Cada tipo de injeção eletrônica possui suas características e suas vantagens. A escolha depende do tipo de motor e das necessidades específicas de cada veículo.
Figura 12 – Funcionamento da Injeção Eletrônica
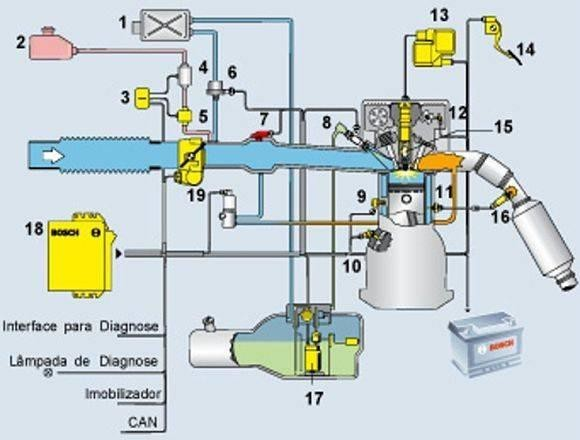
Fonte: PORTAL AUTO (2016)
- Canister,
- Reservatório de gasolina para partidas a frio,
- Relé,
- Bomba elétrica de combustível,
- Válvula solenoide,
- Válvula de purga do canister,
- Sensor de temperatura e pressão do ar,
- Galeria de combustível e Válvula de injeção,
- Sensor de detonação,
- Sensor de rotação,
- Sensor de temperatura,
- Sensor de fase,
- Bobina de ignição,
- Pedal do acelerador,
- Vela de ignição,
- Sonda Lambda,
- Bomba de combustível,
- Unidade de comando;19) Corpo da borboleta.
2.20. INJEÇÃO COMBUSTÍVEL INDIRETA
A injeção indireta de combustível é um sistema para motores de combustão interna que envolve a injeção de combustível no coletor de admissão do motor para que a pressão interna varie entre 3 e 5 bar, em vez de diretamente no cilindro como na injeção direta. Nesse tipo de sistema, a bomba de combustível pressuriza o combustível e o entrega aos injetores localizados no coletor de admissão. O injetor libera combustível na admissão do motor, misturando o combustível com o ar que entra pelo coletor de admissão. A mistura de ar e combustível é então aspirada para os cilindros do motor, onde ocorre a combustão. A injeção indireta de combustível pode oferecer vantagens em relação à injeção direta, como menores custos de produção e manutenção, além de ser mais simples e confiável.
No entanto, a eficiência e a potência do motor podem ser afetadas negativamente porque a mistura ar/combustível pode não ser tão precisa quanto a injeção direta. É importante ressaltar que a injeção de combustível indireta é uma tecnologia antiga e hoje em dia é menos comum, sendo substituída gradualmente pela injeção direta, que oferece melhorias em termos de desempenho e economia de combustível. Para este modelo de injeção, temos dois modos, monoponto e multiponto. Ambos os modos são injeção indireta, no caso, multiponto (MPI) é uma evolução do monoponto.
No sistema de monoponto, o combustível é injetado atrás de um bico só através do coletor de admissão, sendo levado pelo ar e distribuído em cada um dos cilindros, esse sistema a pressão interna fica em torno de 0.5 a 1.0 bar, diferindo muito do carburador, porém tem uma maior precisão e uma mistura mais homogênea, devido a válvula de injeção ser controlada pela ECU (Engine Control Unit – Unidade de Controle do Motor). A ECU é responsável por controlar os atuadores do motor otimizando todo o processo de injeção de combustível, foi programada para trabalhar de forma precisa.
Figura 13 – Injeção Monoponto
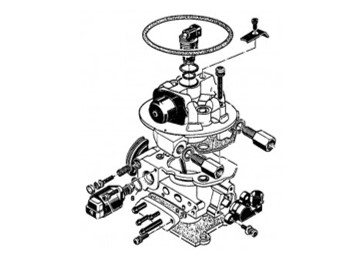
Fonte: ROCHA (2009).
Normalmente conhecida pelas siglas MI, MPI (multi-point injection) e MPFI (multipoint fuel injection), ou como Ford EFI (electronic fuel injection) pela fábrica da Ford, ela está quase sempre associada a uma injeção monoponto. A GM escolheu uma forma mais adequada para seu sistema SFI, já que todas as suas injeções são sequenciais necessitando ser multiponto. No multiponto mais conhecido como MPI, há a presença de um bico para cada cilindro, gerando assim uma melhor curva de potência e torque, com uma média de 15%. Isso se torna possível, pois a mistura passa a ser injetada na entrada das válvulas de admissão, com isso não fica mais aprisionada no caminho”.
Aliado a um coletor de admissão redimensionado, o fluxo de ar menos denso por não estar misturado com o combustível ganha velocidade e o motor atinge uma eficiência volumétrica maior”. No MPI, podemos ter duas divisões, sendo elas sequenciais ou não. No sistema sequencial cada cilindro recebe sua mistura no momento mais adequado em função da ordem de ignição, para a não sequencial, a injeção do combustível ocorro simultaneamente em todos os cilindros, não sendo muito ideal, todavia há casos, como o Corsa, em que o combustível é injetado em dois cilindros ao mesmo tempo, sendo assim chamados de SFI (electronic fuel injection).
Figura 14 – Injeção Multiponto
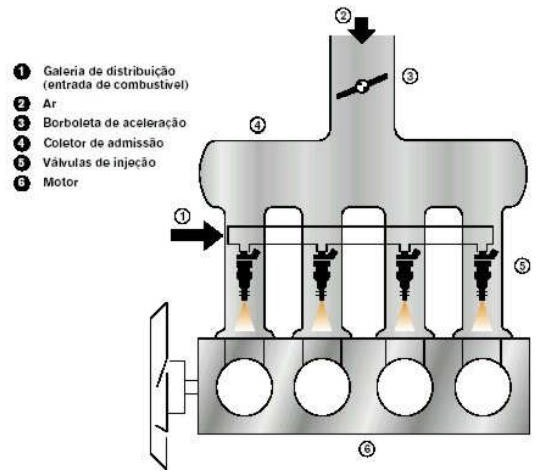
Fonte: CARRO E TÉCNICA (2017).
2.21. SISTEMA COMMOM RAIL
O sistema Commom Rail foi desenvolvido pela FIAT em meados dos anos 90, foi patenteado pela Bosh. Nos anos seguintes esse sistema foi definido como um sistema “tubo comum”, mais eficaz em termos de performance e de utilização de combustível. Para esse sistema, a injeção de combustível se dá através do envio de combustível em um único tubo, como o próprio nome já diz, gerando uma grande pressão. No caso dessa pressão ficar muito alta dentro do tubo, um sistema de retorno foi criado para devolver esse combustível ao tanque. Através do único tubo, o combustível é distribuído para todos os cilindros igualmente, por conta da pressão ser a mesma, pois a bomba de injeção é única, sendo assim, o gasto de energia e de combustível do motor se torna bem menor.
O sistema commom rail é utilizado em sua maior parte em motores que possuem monitoramento de condições dos motores. A partir dos dados coletados como temperatura, pressão do tubo e pressão do pedal, ele regula as válvulas que liberam combustível para cada pistão de forma independente, garantindo que não haja desperdício (CHIPTRONIC, ). A injeção pode ser dívida em pré e pós-injeção, para que haja uma melhora na combustão e eliminando o desperdício.
Figura 15 – Funcionamento Sistema Commom Rail
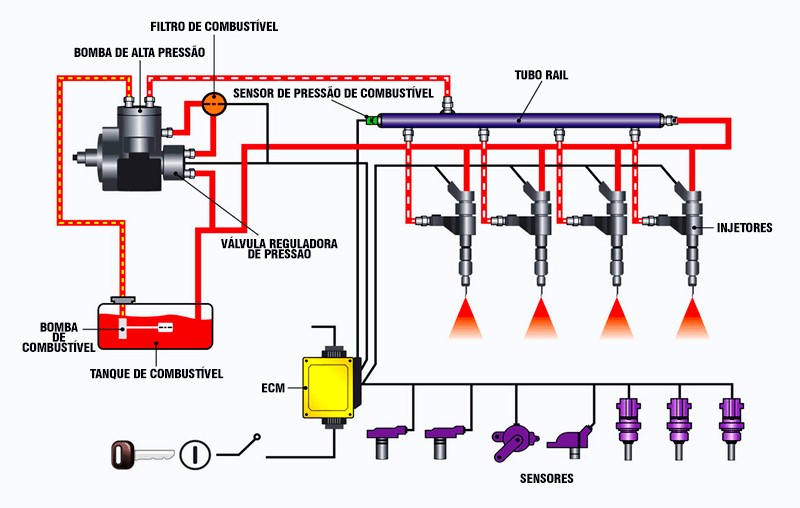
Fonte: GIOROTTI (2021).
Tabela 1- Função de cada componente
Componente | Função |
Régua de injeção | Distribuir uniformemente a pressão estável e o combustível para os injetores, atenuando picos de pressão. |
Válvula controladora de pressão | Limitar pressão atingida pela régua de injeção. |
Injetor | Pulverizar o combustível para dentro da câmara de combustão, atomizando-o. Bomba de alta pressão: Elevar a pressão do combustível. |
Sensor de pressão da régua | Monitorizar a cada instante a pressão atingida na régua. |
Bomba de alimentação | Fornecer combustível a pressão adequada para bom funcionamento do sistema de alta pressão. |
Pré-filtro e Filtro de combustível | Filtrar o combustível para a bomba de alimentação e circuito de alta pressão. |
Tanque de combustível | Armazenar combustível. |
Unidade de comando do motor | Resseção de dados dos vários sensores e aturadores para controlo de todos os componentes |
Fonte: elaborado pelos autores (2023).
A vantagem deste tipo de sistema, está na eficiência no consumo de combustível em relação à performance, devido ao controle da injeção maximizando a combustão, sendo possível um arranque a frio e a obtenção de melhores resultados em baixas rotações. Sendo assim, queimando menos combustível, e esse fica mais econômico, mais eficiente e por sua vez, reduz a emissão de gases poluentes, tornando-se ainda mais ecológico. Esse sistema é mais utilizado em veículos europeus, cada montadora regula seu modo de operação conforme a necessidade exigida pelo local e pelos consumidores, estes podem ser encontrados em veículos de pequeno, médio e grande porte, em sua maioria movidos a diesel (LDAUTO).
2.22. INJEÇÃO DE COMBUSTÍVEL DIRETA
Quando se pensa em injeção direta de combustível, acredita-se que é uma tecnologia nova, e de fato é. E essa tecnologia vem há alguns anos se aprimorando. A nível acadêmico, quem foi o primeiro desenvolvedor deste sistema foi Herbert Akroyd Stuart, ao qual utilizava um sistema parecido com diesel, utilizando uma bomba para pressurizar este combustível com alta pressão ao injetor. Em 1920 este sistema foi aperfeiçoado pela Bosch e Clessie Cummins aos motores a diesel, e assim, revolucionando a história da injeção de combustível (BEÂTA, 2016). Em 1902, o uso precoce da injeção indireta fez com que o engenheiro sueco Jonas Hesselman adaptasse essa tecnologia a motores de aviação, se baseando no modo como o combustível era injetado no final do curso de compressão.
Figura 16 – Primeiro Sistema Injeção Direta
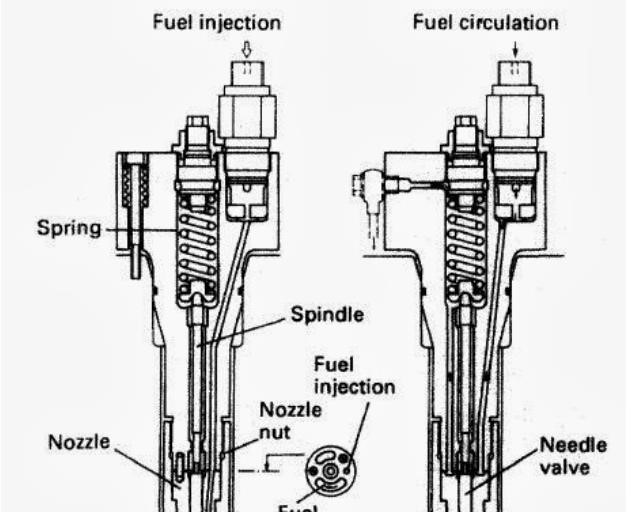
Fonte: BLOG TUNNING PARTS (2014).
Inicialmente testados em carros de corridas, a Alfa Romeo com o motor 6c no 2500 “Ala Space” que obtinha 6 bicos injetores elétricos alimentados pela alta pressão da bomba de combustível.
Figura 17 – Primeiro carro a utilizar Injeção Direta
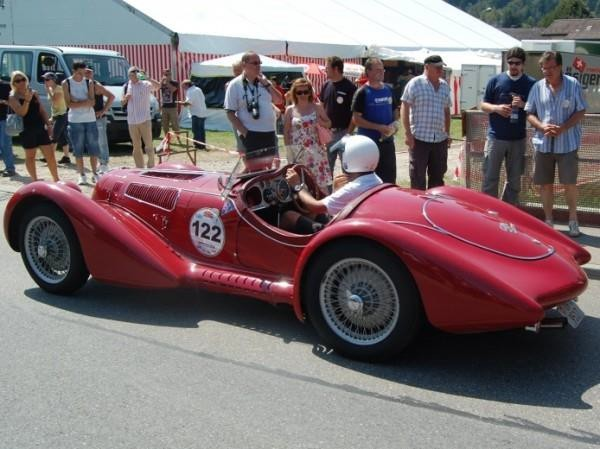
Fonte: BLOG TUNNING PARTS (2014).
O primeiro sistema de injeção de combustível direta de automóvel utilizado para funcionar com gasolina foi desenvolvido pela Bosch, introduzido no Golias GP700 e Gutbrod em 1952 (BEÂTA, 2016). Esse sistema era basicamente construído como um sistema de injeção direta de diesel, utilizando alta pressão com um conjunto de válvulas borboletas à admissão, entretanto usava bomba de gasolina comum para enviar o combustível. A figura abaixo apresenta os sistemas de injeção direta de combustível utilizados na década de 50 e 60.
Figura 18– Sistemas de injeção direta de combustível utilizados na década de 50 e 60
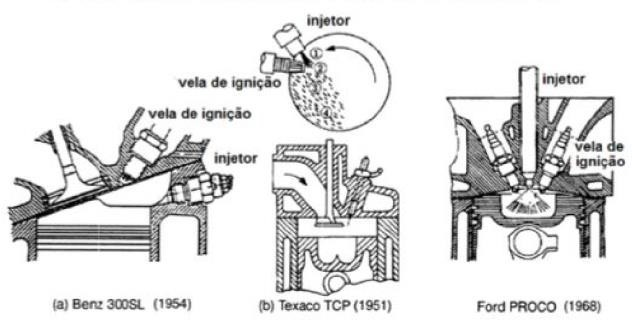
Fonte: CARRO E TÉCNICA (2017).
O primeiro motor com injeção direta de linha a ser comercializado foi produzido no mercado japonês em 1996 (ZHAO, 2010).
Figura 19– Primeiro sistema de injeção direta usado em linha de produção
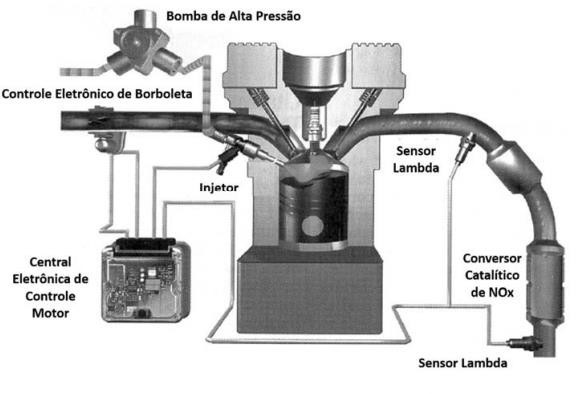
Fonte: ZHAO (2010).
Os primeiros motores com injeção direta, não tiveram uma boa aceitação, já que não atingiam níveis de eficiência esperados. Outro grande fator decisivo para o não alcance de vendas desses motores, foi o modo como ele foi projetado, trabalhando com sistemas de injeção de mistura Wall-Guided ou Air-Guided, operando assim com misturas estratificadas e pobres somente em uma determinada faixa de funcionamento do motor. Segundo Zhao (2010), essas restrições, juntamente com um completo sistema de pós-tratamento de gases expelidos pelo escapamento, em conjunto com misturas pobres, levaram ao desenvolvimento de sistema de injeção direta empregando misturas estequiométricas e homogêneas.
Somente em 2006 foi introduzido no mercado um sistema de injeção direta mais sólido e conciso. Criado pela BMW e pela Mercedes-Benz esse motor conseguia operar com misturas pobres por uma ampla faixa de funcionamento, o que acarretou uma economia de 10 a 20%, se compararmos com o MPI, isso se deu por conta do novo modelo de sistema chamado Spray-Guided. Com esta tecnologia aliada à alimentação e à tecnologia de downsizing, atualmente foi possível chegar a níveis altíssimos de eficiência e desempenho. O sistema de GDI é mais eficiente do que o MPI, devido ao modo como o combustível entra na câmara de combustão, neste sistema ele é injetado direto na câmara sob pressão.
Em grande parte de sua concepção este sistema se assemelha ao MPI, porém com alguns componentes diferentes, como por exemplo: Bombas de alta pressão, o próprio injetor, sensor de controle fluxo, sensores de fase no eixo comendo e sensor de temperatura no sistema de descarga. Conforme Bosch (2006), este sistema necessita de uma pressão bem mais robusta para seu trabalho e devido a isso utiliza-se uma pressão entre 50 a 200bar, conforme figura 20:
Figura 20– Sistema de injeção direta desenvolvido pela Bosch.
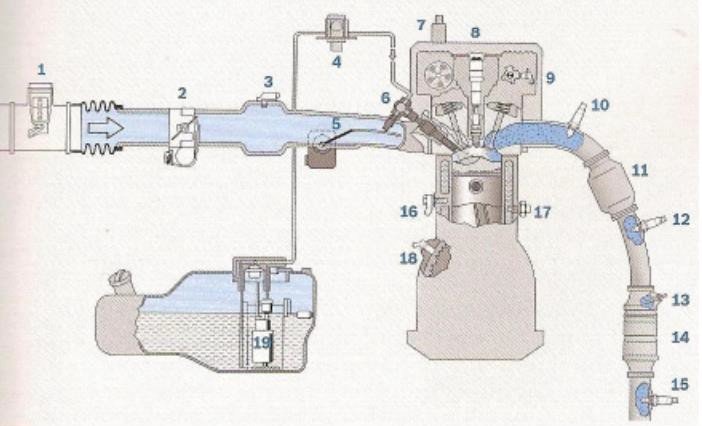
Fonte: BOSCH (2006, p. 119).
2.23. MISTURA HOMOGÊNEA E ESTRATIFICADA
É possível afirmar que o sistema de injeção direta trabalha com dois tipos de mistura, como já citado anteriormente: homogênea e estratificada. Em casos que se utilizam de mistura homogênea, esse combustível é injetado no cilindro durante a fase de admissão do ar somado ao tempo de exposição desse combustível dentro da câmara, e como resultado ocorre uma mistura completa de ar / combustível, gerando uma variação desprezível ao fator lambda. Neste sistema, o combustível é controlado de forma sob demanda, na qual haverá uma vazão e pressão determinada. Utilizando-se de duas bombas de combustível: uma elétrica posicionada no tanque do veículo e uma mecânica com alta pressão posicionada no cabeçote com o acionamento pelo came do comando de válvulas.
A bomba elétrica é controlada por um módulo PWM (significa modulação por largura de pulso, isso quer dizer que é possível variar a intensidade do sinal alterando a largura de cada pulso), podendo assim controlar a vazão da bomba, consequentemente variando a pressão da linha (em torno de 3 a 6bar) em função do pulso, esta pressão (mecânica online). Por sua vez a bomba mecânica recebe o combustível enviado passando por uma válvula reguladora, liberando assim de forma controlada, o funcionamento do motor, controlando a pressão de cada injetor, na qual fica para marcha lenta uma média de 50bar e para carga plena 110 bar.
Figura 21 – Mistura Homogênea
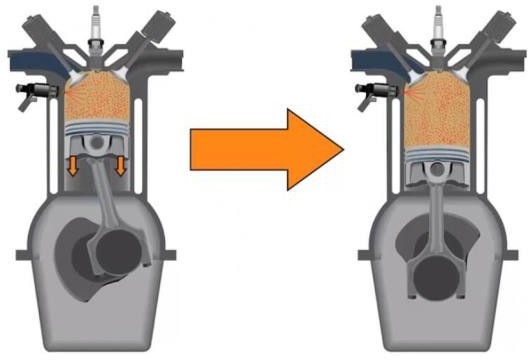
Fonte: DOUTOR IE (2023).
Já na mistura estratificada, há dois modos de operação, conhecida como Split Injection, que trabalha na admissão do ar e depois com compressão ou é injetado somente na fase de compressão, ou seja, o pistão inicia o trabalho sem ar. Sendo assim, este combustível que foi injetado dentro da câmara de combustão não se mistura por completo, variando muito o fator lambda, e com isso consegue-se trabalhar de forma mais ampla em uma mistura mais pobre (ZHAO, 2010). Esta situação faz com que essa mistura se torne mais explosiva sem precisar de uma quantidade de combustível maior, pois está mais concentrado perto da vela.
Figura 22 – Mistura Estratificada
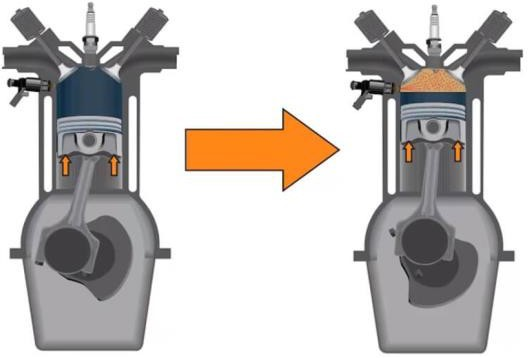
Fonte: DOUTOR IE (2023).
Figura 23 – Comparação entre mistura Homogênea e Estratificada
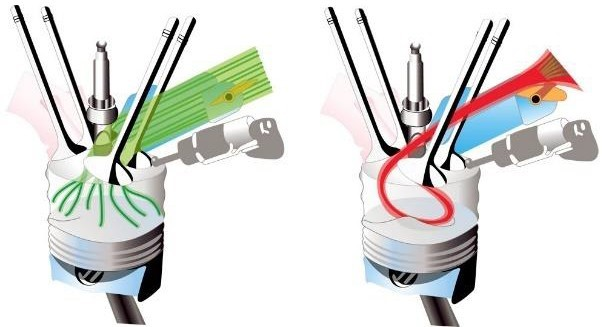
Fonte: TROIA GÁS (2023).
Fator Lambda
O sensor da sonda lambda, conhecido pela letra grega (λ) é responsável por medir a relação estequiométrica entre a quantidade ideal de combustível em relação ao ar admitido. Este sensor geralmente está acoplado à parte de escapamento do veículo, em que mede a relação entre ar / combustível. Esta relação pode ser calculada através da fórmula:

Trabalhando em uma escala de 0 a 1, em que 1 seria uma mistura ideal e quanto mais próximo de 0 mais pobre. Atualmente a maior parte do setor automotivo trabalha com o lambda muito próximo de 1, pois este é a condição perfeita para se obter uma melhor eficiência e economia.
Figura 24 – Relação entre Sonda e trabalho ideal
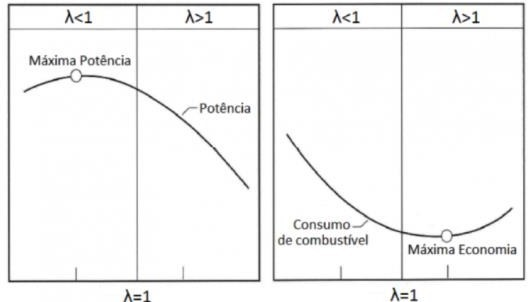
Fonte: PRO TUNE (2016).
A injeção direta tem três modelos de sistema: Wall-Guided, Air-Guided, SprayGuided:
• SISTEMA WALL-GUIDED
A injeção de combustível Wall-Guided é um tipo de sistema de injeção de combustível usado em alguns motores de combustão interna. Neste sistema, os injetores são colocados próximos à parede do cilindro, e o combustível é pulverizado na direção da parede do cilindro ao comando diretamente na câmara de combustão. O sistema Wall-Guided foi projetado para promover uma melhor mistura de combustível e ar na câmara de combustão. Ao pulverizar combustível contra as paredes do cilindro, as gotas de combustível são quebradas em partículas menores e se misturam mais facilmente com o ar contido no interior da câmara de combustão. Obtendo como resultado uma queima mais assertiva e ajustada e uma melhora na eficiência do motor.
Este sistema também ajuda a reduzir as emissões, especialmente de óxidos (NOx). Isso ocorre porque o modo de injeção de combustível contribui para um ambiente de combustão mais frio, o que reduz o acúmulo de óxidos de emissão. No geral, os sistemas de injeção de combustível guiados por parede são um dos vários tipos de sistemas de injeção de combustível que podem ser usados em sistemas de injeção de combustível guiados por parede. Em motores de combustão interna, seus benefícios incluem: maior eficiência do motor e emissões reduzidas, embora também possa exigir um ajuste mais fino do motor para obter um desempenho ideal.
Figura 25 – Sistema Wall-Guided
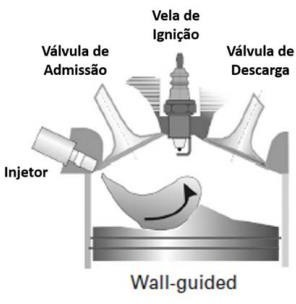
Fonte: ZHAOS (2010).
Porém, segundo Zhao (2010), este sistema não teve um alcance muito significativo, pois a redução do consumo de combustível não atingiu razões significativas, pelas seguintes razões:
- O transporte de mistura está diretamente ligado à posição do pistão, assim torna-se difícilcoordenar adequadamente o instante da injeção e de ignição em uma ampla faixa de operação do motor;
- Os pórticos para swirl e tumble requeridos para produzir a desejada estrutura de fluxoinfluencia negativamente a mistura em altas cargas;
- O combustível depositado nas paredes do cilindro e no pistão propicia a formação de filmefluido e resulta em uma combustão incompleta. A formação de fuligem e depósitos nessas regiões, trazem como consequência o aumento das emissões de hidrocarbonetos;
- Há entrada de combustível na região de squish na câmara de combustão. Em transições debaixa para alta, carga é necessário injetar mais combustível e ajustar o instante de injeção e ignição para maximizar a eficiência de conversão de combustível. Contudo, o combustível injetado nessas condições pode penetrar a região de squish na câmara de combustão. Nesse caso, uma vez que o combustível não é totalmente queimado, as emissões de hidrocarbonetos são maiores;
- As perdas mecânicas são maiores. O pistão empregado a esse sistema é mais largo e maispesado que um pistão convencional devido sua geometria especial, aumentando a inércia do conjunto rotativo e reduzindo assim a eficiência mecânica.
SISTEMA AIR-GUIDED
A injeção de combustível direta air-guided é um sistema de injeção de combustível em motores a combustão interna que utiliza um design de câmara de combustão com fluxo de ar guiado para melhorar a eficiência da combustão e reduzir as emissões. Neste sistema, utilizam-se estruturas de fluxo para fazer a mistura ar-combustível, utilizando a parte de cima do pistão para ajudar na formação da estrutura e do fluxo. Sendo assim, o sucesso deste sistema está ligado diretamente à orientação do jato de combustível. Para este sistema é muito importante garantir que a mistura fique próxima da vela de ignição na parte fase de compressão.
Segundo Zhao (2010), o swirl e tumble deste sistema reduzem a eficiência volumétrica, sendo assim influenciando negativamente o desempenho do motor. Mas conhecido como sistema de primeira geração, temos uma relação entre sistema wall/air guided, que utilizam as estruturas de fluxo para direcionar a mistura ar-combustível, dificultando assim a distinção dos mesmos.
Figura 26 – Sistema Air Guided

Fonte: ZHAOS (2010).
• SISTEMA SPRAY GUIDED
O sistema de injeção direta por spray guiado é considerado uma segunda geração do sistema de injeção direta. Uma característica importante do sistema é a vela de ignição que está perto do injetor de combustível. Essa intimidade deve ser garantida pelo posicionamento ideal da vela de ignição em relação à “nuvem” combustível produzido pelo injetor, possibilitando a ignição da mistura ampla faixa de operação do motor. O fator decisivo para este sistema está relacionado às características seringa. Os injetores devem produzir um padrão de injeção de combustível robusto e confiável ciclo a ciclo, estável durante a operação do motor, mesmo sob mudanças na contrapressão ou na estrutura do fluxo dentro do cilindro para o bem na operação do sistema de orientação de pulverização.
Alguns aspectos devem ser observados por exemplo: carbonização de velas de ignição e injetores e tolerâncias modo de injeção de combustível. Se o combustível for submetido a choque térmico da vela de ignição o líquido entra em contato com ele, afetando o efeito da rotação do motor, condições de fluxo perto da vela de ignição e tempo curto preparação da mistura pré-faísca (ZHAOS, 2010). Ao comparar sistemas de orientação de pulverização com sistemas de primeira geração, a formação de um filme de fluido no pistão ou na parede da câmara de combustão é muito reduzida a ponto de ser eliminada continuamente, as emissões de hidrocarbonetos são reduzidas.
Uma vez que o sistema de orientação da pulverização não requer uma estrutura de fluxo específica para entregar a mistura à vela de ignição, turbulência no cilindro para auxiliar na propagação chama, produzindo combustão rápida em toda a faixa de operação do motor dar mudanças repentinas de baixa carga para alta carga em sistemas tradicionais, existem ligeiro atraso na resposta do motor devido ao tempo de enchimento sistema de admissão de ar e cilindros com admissão de ar estratégia de carregamento após a estratificação, o motor funciona com o corpo do acelerador totalmente engatado, o tempo de resposta do motor às solicitações de torque é reduzido (ZHAOS, 2010).
As vantagens termodinâmicas da injeção direta podem ser vistas rapidamente comprovado pela análise de perda de energia, sob condições de carga parcial. Aumentar o índice multipartidário resulta em vantagens consideráveis em relação aos motores que utilizam misturas pré-misturadas. Quando comparado a um motor PFI com operação parcial do corpo do acelerador ligada, a injeção direta de combustível também reduz consideravelmente o trabalho de bombeamento. Nos motores de injeção direta, operando com carga estratificada, o aumento de temperatura no final da compressão é devido à alta concentração de gás misto e alta taxa de compressão.
Como o calor flui para as paredes da câmara de combustão ocorrendo mais fortemente perto do PMS, as perdas de transferência de calor são maiores neste sistema em comparação com o motor. O sistema PFI opera sob condições estequiométricas, embora a temperatura e o tamanho médio da câmara de combustão de um sistema de injeção direta seja menor. O sistema injeção direta tem outras desvantagens, como maior atrito e maior a energia necessária para acionar a bomba de combustível de alta pressão (ZHAO, 2010).
Figura 27 – Sistema, Spray Guided
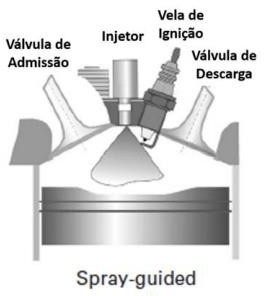
Fonte: ZHAOS (2010).
Figura 28 – Comparação entre primeira e segunda gerações
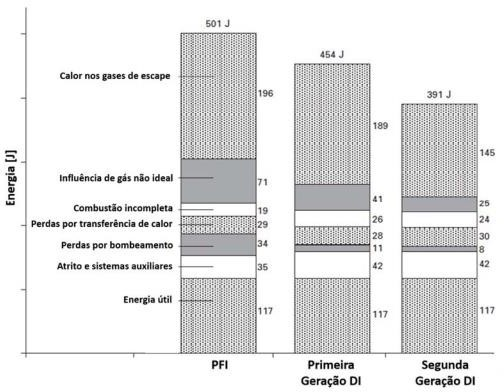
Fonte: ZHAOS (2010).
2.24. BICOS DE INJEÇÃO DIRETA
Atualmente, são utilizados três tipos injetores de combustível para injeção direta. Os injetores podem ser diferenciados entre si pela forma como se abrem e fecham. O injetor de abertura externa (A – Nozzles) expõe a seção transversal do bico quando a válvula abre e gera a autoformação do jato de combustível por meio de um cone. O injetor multifuro e o injetor do tipo swirl são ambos de conceito de abertura interna (I – Nozzles) (ZHAO, 2010).
Figura 29 – Tipos de bico injetor
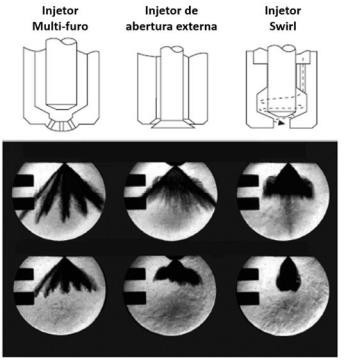
Fonte: ZHAOS (2010).
O injetor espiral é de boa e alta qualidade de atomização, injeção de combustível flexível, baixa sensibilidade à poluição e distúrbios mecânicos e térmicos. É uma injeção relativamente acessível até agora produzida em massa. A injeção de combustível começa a partir deste injetor, o combustível é pré-injetado e então um cone oco é formado o ângulo do cone, a formação do jato é fortemente afetada pela contrapressão e combustão atualmente, esse tipo de injetor é utilizado em sistemas de injeção direta. Camadas homogêneas de mistura e rejunte com sistema de guia de parede. A maior desvantagem em comparação com os sistemas de sprinklers guiados é a localização Injetor e vela de ignição (ZHAOS, 2010).
Injetor multi-furos com injeção de combustível claramente definido. Devido à atomização insuficiente do orifício poroso, apenas uma mistura parcialmente homogênea pode ser criada na câmara de mistura. Combustão, excesso de áreas e hiperespaços no perfil de combustível da aeronave, escassez de combustível. Então, quando o processo ao queimar, a frente de chama não é distribuída uniformemente pela câmara de combustão. Queimando, acelerando sua propagação pela área apendicular de combustível e reduzi-lo em áreas de escassez de combustível. Então o número de orifícios no injetor tem um impacto significativo em suas características operacionais Motor (ZHAOS, 2010).
A comparação de transmitância combustível entre os injetores de redemoinho e os coletores. Penetração de armas o tipo poroso é superior aos injetores de vórtex, que é uma característica que vale a pena considerar cuidados ao calibrar um motor com este tipo de injetor, pressão e tempo de injeção. Injetor Vórtex com pré-injeção suas características de trabalho. A presença dessa pré-injeção afeta a quantidade de combustível injetado nos cilindros e emissões ciclo a ciclo hidrocarbonetos, se este jato dianteiro atingir a superfície do pistão por sua maior causa avanço. A penetração do jato do injetor de abertura externa é menor no consumo de combustível do que vários injetores. Em comparação com injeções tipo Vortex, têm a vantagem de produzir um cone oco mais uniforme que a geração anterior de aeronaves a jato.
A contrapressão da câmara de combustão tem pouco efeito no ângulo Símbolo de contorno do cone. Este tipo de injetor combinado com um atuador piezoelétrico elétrico, fornece múltiplas injeções de combustível em rajadas curtas, o que o torna superior aos sistemas tradicionais de válvulas solenoides. Tiro de abertura ao ar livre são uma escolha atraente para sistemas de guia de sprinklers porque tem sensibilidade da bobina plana (ZHAOS, 2010).
Figura 30 – Relação entre tipos de bico e tempo de abertura
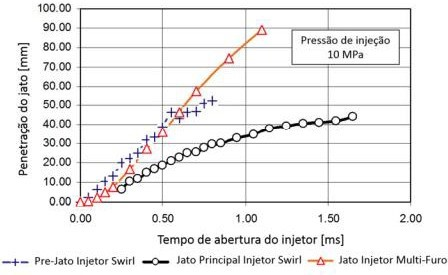
Fonte: BAETA (2012).
2.25. TURBO – COMPRESSORES
A máxima potência gerada por um motor é calculada através da admissão de combustível que pode ser queimada eficientemente dentro do cilindro, o que significa que a quantidade de ar é introduzida em cada etapa do ciclo. Caso essa quantidade de ar comprimido admitida tiver maior densidade que nas condições ambientes antes de entrar no cilindro, a potência máxima será maior. Através de um turbo compressor ou superchargers a potência pode ser aumentada. O turbo, pode ser definido como um compressor centrífugo com uma turbina acionada pelos gases de escapamento, aumentando a pressão admitida, esta admissão está ligada diretamente a velocidade de rotação do motor.
O turbo compresso foi inventado em 1905, pelo suíço Alfred Buchi. De 1918 a 1925, a Royal Aircraft Factory fez experimentos com turbos em aviões, porém sem sucesso. A primeira aplicação de turbo compressores em carros, aconteceu em 1923, quando Major Frank, piloto de avião e de carros, equipou um motor de 1.5L e 6 cilindros em linha. Estas aplicações foram vistas em linha em embarcações movidas a diesel por volta do ano de 1925. Entre 1962 e 1963, a empresa Olsdmobile e a Chevrolet apareceram com os primeiros carros equipados com sistemas de sobre alimentação (ZHAO, 2010). Em 1973 dando início a “era turbo”. A fórmula 1 trouxe os primeiros motores equipados com turbo compressores, onde teve um tempo de duração até meados de 1989, já em retornou à categoria.
O turbo compressores que consistiam em uma unidade central chamada carcaça central e um conjunto rotativo (CCCR) do inglês Central Housing and Rotating Assembly CHRA, uma turbina, um compressor e o atuador. Tanto o rotor do compressor quanto o da turbina são montados e fixados em um eixo que os interliga através de rolamentos radiais e rolamentos axiais. Através dos gases expelidos pelo escapamento no rotor da turbina geram energia cinética rotacional. Esta energia que fora produzida aciona o rotor compressor através de eixo mancal, sendo assim comprime o ar admitido pelo motor (SHAFER, 2015).
Figura 31 – Funcionamento de um turbocompressor
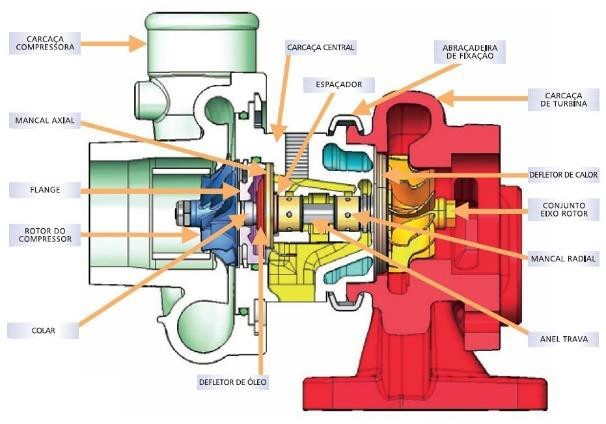
Fonte: MASTERPOWER (2014).
Atualmente presente na maioria dos motores que utilizam o conceito de downsizing (menor cilindrada com maior eficiência), os turbos compressores recuperam a potência perdida pelo deslocamento do volume. Estes apresentam reduções no consumo de combustível entre 15 a 18% hidrocarbonetos e 12 a 18% de nitrogênio, estes são tão eficientes que chegam a valores de 40% (BEÂTA et al, 2015; BORETI, 2012; FRASE et al., 2009). Para o dimensionamento do turbo compressor é utilizado a aplicação do motor juntamente com a faixa de operação determinada. Através das características do motor como potência máxima gerada, volume deslocado, rotação da potência máxima, conseguimos determinar as dimensões e os parâmetros do turbo compressor.
Figura 32 – Características de um turbocompressor
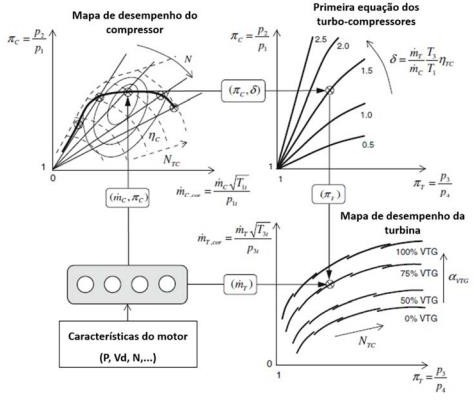
Fonte: SHAFER (2015).
Através da energia cinética vencida o eixo e rotor entram em funcionamento. Este intervalo necessita atingir o torque máximo do motor, a partir da marcha lenta. Chamado de lag ou turbolag é definido pelo tempo de resposta do t90 (90% do torque máximo) intervalo de tempo, necessário para atingir a aceleração do motor.
Figura 33– Tempo de resposta de um turbo
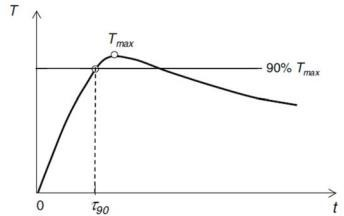
Fonte: SHAFER (2015).
Motores com turbo compressores maiores possuem maior inércia para altas rotações, o que pode acarretar um turbolag maior, devido a sua maior resistência a inércia mecânica, devido ao baixo torque produzido nas baixas rotações. Para diminuir este efeito, utiliza-se um modo chamado Twin-charge ou turbo compond. O Twin charge consiste em dois turbos compressores acoplados no motor, o primeiro de menor tamanho, trazendo uma melhor resposta em baixas rotações e um maior, responsável pelo maior torque em altas rotações. Entre 1000 a 5000 RPM a razão de ar passada pelos compressores chegam entre 2,5 a 2,8, esta eficiência chega a alcançar valores 44% na conversão de combustível (BEÂTA et al, 2015). Os Twin chargers híbridos são mais utilizados para minimizar o turbolag gerando altos torques instantaneamente.
Figura 34 – Funcionamento de um Turbo Twin chargers
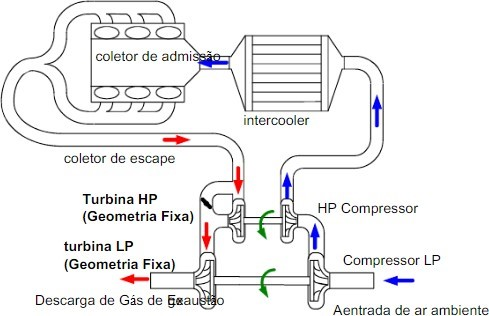
Fonte: MOTOR SPORT (2017).
É possível correlacionar o turbo compressor com a injeção direta de três formas principais. A primeira é a carga mecânica que esse motor é submetido, a carga calorífica que esse motor é exposto e os níveis de poluentes emitidos por ele. A adição de um turbocompressor ao motor permite um aumento significativo na pressão do ar admitido na câmara de combustão, o que resulta em uma maior densidade de ar disponível para a combustão. Isso, por sua vez, leva a uma maior potência do motor, já que uma maior quantidade de oxigênio disponível permite uma queima de combustível mais eficiente e maior produção de energia. A injeção direta de combustível permite que o combustível seja injetado diretamente na câmara de combustão, em vez de passar pelo coletor de admissão.
Isso permite um controle mais preciso da mistura ar/combustível, o que pode levar a uma combustão mais completa e eficiente. Combinado ao aumento da pressão do ar fornecido pelo turbocompressor, a combinação de injeção direta de combustível e da turbo-alimentação pode resultar em uma melhor eficiência de combustível em comparação com motores aspirados naturalmente.
Os turbocompressores são capazes de fornecer um aumento instantâneo de potência quando o acelerador é pressionado, devido ao aumento imediato da pressão do ar admitido na câmara de combustão. Isso resulta em uma resposta rápida do acelerador e uma aceleração mais vigorosa, tornando a condução mais esportiva e emocionante. Melhor desempenho em altitudes elevadas: Os motores turbocomprimidos são especialmente eficazes em altitudes elevadas, onde a densidade do ar é menor. A pressão de ar aumentada pelo turbocompressor compensa a menor densidade do ar, permitindo que o motor mantenha seu desempenho e potência mesmo em altitudes elevadas.
A injeção direta de combustível permite um controle mais preciso da mistura ar/combustível, o que pode ajudar a reduzir as emissões de poluentes, como óxidos de nitrogênio (Nox) e partículas de combustível não queimado. Além disso, o aumento da eficiência de combustível proporcionado pela combinação de turbocompressores e a injeção direta de combustível pode contribuir para a redução das emissões de dióxido de carbono
(CO2).
Em resumo, a combinação de turbo compressores e a injeção direta de combustível em motores de combustão interna oferece uma série de vantagens, incluindo maior potência, melhor eficiência de combustível, resposta rápida do acelerador, melhor desempenho em altitudes elevadas e potencial para redução de emissões. Essa combinação é amplamente utilizada em muitos motores modernos, especialmente em veículos de alto desempenho e motores de última geração, para otimizar o desempenho e a eficiência do motor.
2.26. EIXO COMANDO CVVT
Figura 35– Eixo comando CVVT
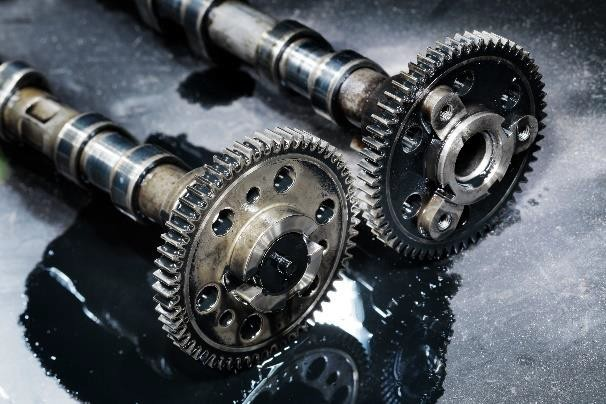
Fonte: CANAL DA PEÇA (2017).
O eixo comando possibilita um fino ajuste entre o tempo entre as válvulas e o virabrequim, em um motor de combustão interna. Neste sistema, existem alguns deles que somente atuam nas válvulas de admissão e sistema que atuam somente nas válvulas de descarga ou também, temos o caso daqueles que são utilizados em ambos os casos. Este ajuste de fases, nos permite reduzir a emissão de poluentes e do consumo, além de aumentar o torque, potência e o conforto quando o motor se encontra em marcha lenta. Sua faixa de trabalho está normalmente entre 20° a 30° no comando, resultando em um ajuste de 40° a 60° no virabrequim. Para esses sistemas existem tanto ajuste de corrente quanto por correia dentada.
Figura 36 – Conceitos e vantagens do comando CVVT
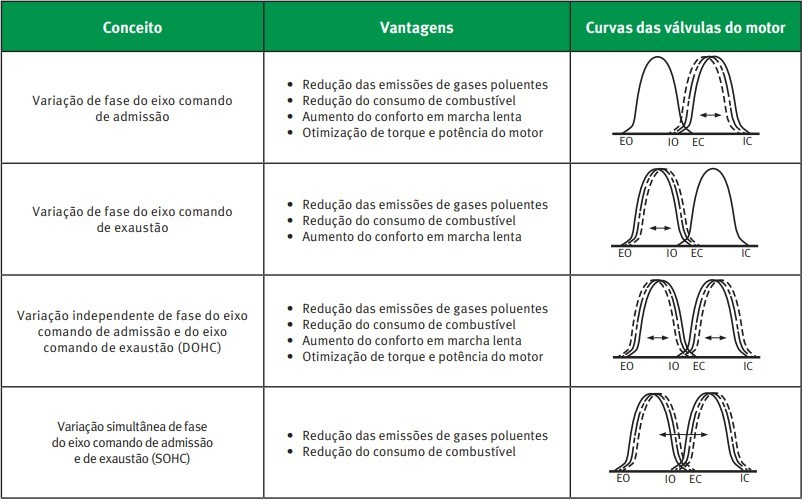
Fonte: SCHAEFFLER BRASIL LIDA (2011).
Segundo Bonatesta et al. (2016), o uso de sistemas CVVT em motores de injeção direta e indireta aumenta o consumo em 5% a 8%. Uma relação linear é introduzida entre a operação do motor operando em diferentes condições. Um aumento de 6% na potência e um aumento de 13% no consumo de combustível (BONATESTA et al., 2016). Uma boa relação é estabelecida entre o ângulo máximo de velocidade do pistão e o ângulo máximo de deslocamento da válvula de admissão em cada condição de rotação, resultando em melhor eficiência volumétrica (TITOLO, 1991).
Figura 37 – Relação de variação do comando
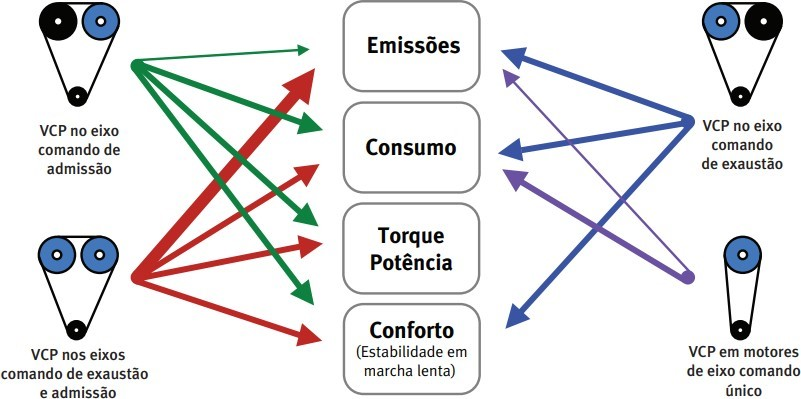
Fonte: SCHAEFFLER BRASIL LIDA (2011).
2.27. RELAÇÃO ENTRE INJEÇÃO DIRETA E REDUÇÃO DE EMISSÃO DE GASES POLUENTES
É importante destacar que o cumprimento das normas regulamentadoras de emissões de gases é uma responsabilidade dos fabricantes de veículos, que devem projetar e produzir veículos que atendam aos limites estabelecidos. A injeção direta de combustível é uma tecnologia que pode contribuir para esse objetivo, mas também é importante considerar outras tecnologias e estratégias de controle de emissões, que devem ser usadas em conjunto, para alcançar um melhor desempenho ambiental para os veículos.
3. Materiais e Métodos ou Metodologia
A fim de compor ação dos resultados foi realizada uma comparação entre o motor de ciclo Otto com 4 cilindros com injeção indireta multiponto com o motor de injeção direta sobrealimentado. Para isso, será usado como base comparativa o motor 1.6 16v da Hyundai (Gamma), que neste caso seria um motor dianteiro, situado numa disposição transversal de 4 cilindros, com tuchos mecânicos, duplo comando, o que faz com que o carro se torne 16v, aspirado, acionado por uma corrente.
Figura 38– Motor Gamma
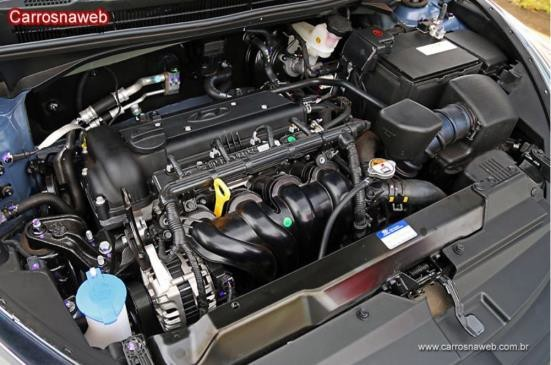
Fonte: CARROS NA WEB (2020).
O motor da Hyundai será comparado ao motor 1.0 Turbo GDI (Kappa), neste motor dianteiro, na disposição transversal de 3 cilindros em linha, com tuchos mecânicos, duplo comando, com variações na admissão e no escape, acionado por uma corrente e sobre alimentado por um turbo compressor.
Figura 39 – Motor Kappa
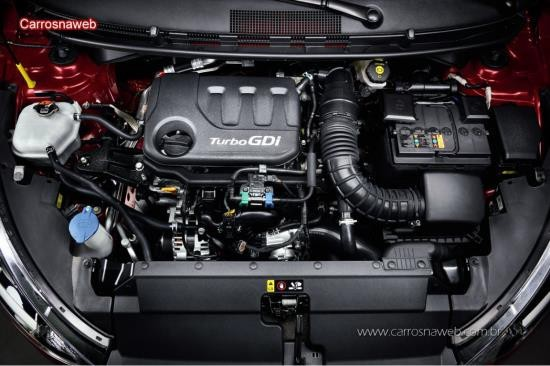
Fonte: CARROS NA WEB (2020).
Como comparativo foram usados os dados obtidos através de uma pesquisa de consumo e eficiência energética desses veículos disponibilizada pelo INMETRO.
4. Resultados e discussão
A partir destes dados foram gerados dois gráficos com resultados de emissão de poluentes no Microsoft Excel. A base dessas normas é a euro, que se assemelha muito ao que temos vigente no Brasil.
Figura 40 – Relação entre motor Gamma e Norma Euro 4
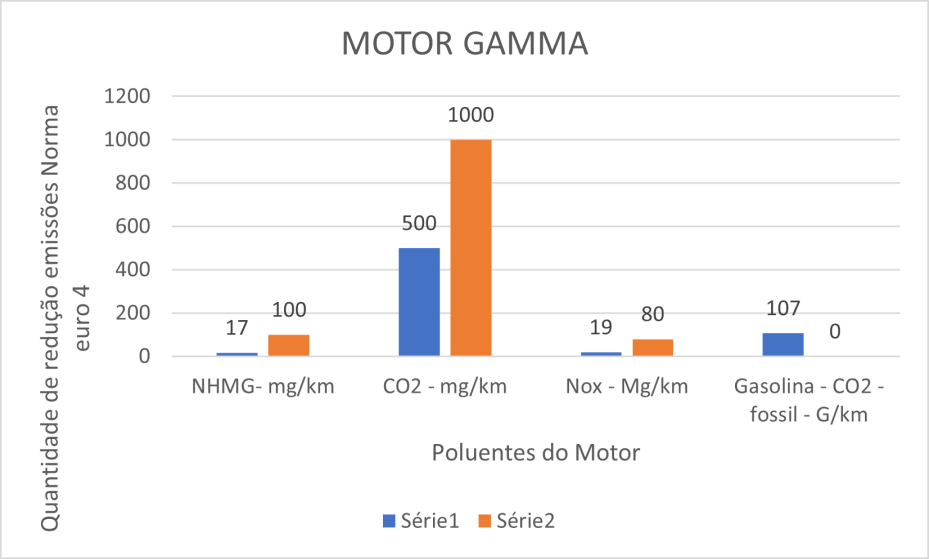
Fonte: elaborado pelos autores (2023).
Poluentes emitidos pelo motor Gamma com injeção indireta, obtém 17 mg/km de hidrocarbonetos não-metânicos emitidos. A taxa de Dióxido de Carbono (CO2) apresentada na norma é de 1000, mas o motor emite 500 mg/km. Quanto aos óxidos de nitrogênio a norma exige a emissão de 80, em contrapartida, o motor emite 19 mg/km de óxido de nitrogênio. A gasolina é emitida em 107 g/km em emissão a partir do escapamento.
Figura 41 – Relação entre motor Kappa e Norma Euro 4
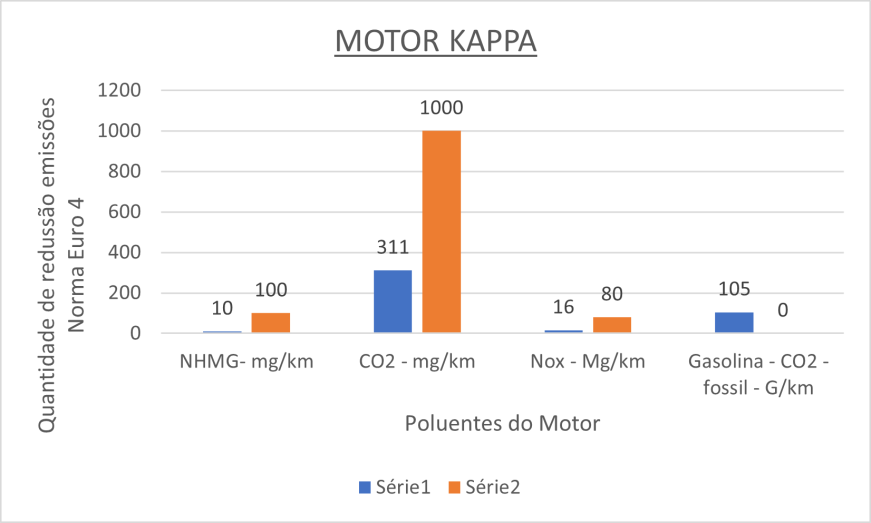
Fonte: elaborado pelos autores (2023).
Poluentes emitidos pelo motor Kappa com injeção direta sobre alimentado por um turbo compressor, obtém 10 mg/km de hidrocarbonetos não-metânicos emitidos. A taxa de Dióxido de Carbono (CO2) apresentada na norma é de 1000, mas o motor emite 311 mg/km. Quanto aos óxidos de nitrogênio a norma exige a emissão de 80, em contrapartida, o motor emite 16 mg/km de óxido de nitrogênio. A gasolina é emitida em 105 g/km em emissão a partir do escapamento, o que representa um nível muito abaixo.
Figura 42 – Relação entre Motor Gamma e Kappa
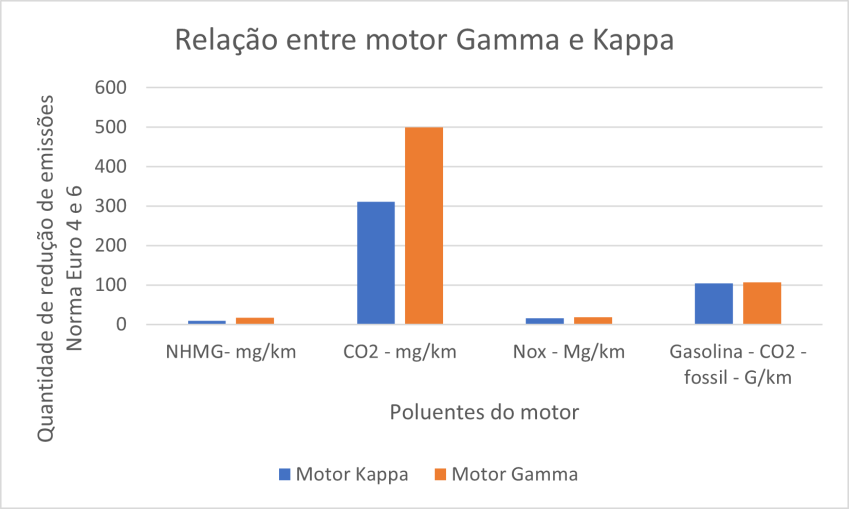
Fonte: elaborado pelos autores (2023).
Na comparação atual, podemos ver que o motor Gama emite mais poluentes do que o motor Kappa, e sua eficiência energética é muito menor. A potência desenvolvida pela tecnologia GDI é muito grande, o que traz maior eficiência energética ao motor e reduz a quantidade de emissão de poluentes, sendo assim, contribuindo com o efeito estufa e com a camada de ozônio. O carro elétrico pode não ser a solução definitiva para um futuro mais limpo. Por mais que os carros elétricos contribuam para o bem do meio ambiente, pois é movido a base de energia sustentável, ela agride a camada de ozônio, levando a sua destruição, o que seria fatal aos seres humanos e outros animais. Além disso, também foi visto que os carros elétricos geralmente emitem muito dióxido de carbono, o que pode levar a uma intensificação do efeito estufa.
No Brasil, 85% da matriz energética é renovável (um dos maiores percentuais do mundo), a pegada de carbono do ciclo de um elétrico é bem menor em relação a outros países do mundo, de acordo com o estudo da Mahle (2020) para produção de eletricidade no Brasil são geradas 17,6 toneladas em dez anos, um percentual acima da emissão da queima do etanol (12,1 toneladas/10 anos). Ao contrário do que vem sendo defendido pela maioria das montadoras, especialmente as europeias, o veículo elétrico a bateria deve ser apenas uma transição, por não resolver os problemas ambientais. Com a adição do atual downsizing (turbo e injeção direta de combustível) podem-se obter números ainda menores nas emissões de CO2 em comparação aos sistemas de injeção de combustível tradicionais (injeção multiponto indireta MPI), pois esse sistema permite trabalhar com misturas mais precisas e com melhor aproveitamento do combustível. Portanto, mesmo com tecnologias mais modernas e atuais, o uso do etanol ainda se configura como a melhor das opções, e também a energia mais limpa.
5. Considerações Finais
Com este estudo foi possível concluir que a combinação de injeção direta de combustível e motores turboalimentados utilizando etanol como combustível pode oferecer inúmeros benefícios termos de desempenho e eficiência dos veículos. A injeção direta de combustível é um sistema em que o combustível é injetado diretamente no cilindro do motor ao invés de passar pelos dutos de admissão e isso acaba permitindo um controle mais preciso sobre a quantidade e acerca do momento da injeção, resultando em uma combustão mais eficiente. Os motores turboalimentados, por sua vez, utilizam um turbocompressor para aumentar a quantidade de ar admitida no cilindro, isso permite que mais combustível seja queimado, o que resulta em maior potência e torque em comparação com motores aspirados de tamanho similar.
Quando a injeção direta de combustível é combinada com motores turboalimentados, especialmente utilizando o etanol como combustível, é possível obter um melhor desempenho. Com o turboalimentado, o motor recebe uma maior quantidade de ar, permitindo a queima de mais combustível e gerando um aumento significativo de potência em relação a motores aspirados. Além disso, foi vista uma eficiência aprimorada, onde a injeção direta de combustível contribui para uma melhor eficiência energética, uma vez que o combustível é injetado diretamente no cilindro, evitando perdas de calor e mistura inadequada. O etanol é um combustível que possui uma alta octanagem, o que permite taxas de compressão mais altas, resultando em uma combustão mais eficiente e aumento da eficiência térmica do motor.
Outro benefício é a redução de emissões de gases poluentes para a atmosfera, o etanol é considerado um combustível mais limpo em relação à gasolina, diesel, a outros combustíveis fósseis e melhor do que utilizar da eletricidade para movimento do veículo (carros elétricos), por possuir uma menor quantidade de carbono em sua composição. Quando utilizado com a injeção direta de combustível e motores turboalimentados, o etanol pode ajudar a reduzir as emissões de gases poluentes, como dióxido de carbono (CO2) e óxidos de nitrogênio (NOx). É importante ressaltar que a eficácia dessas tecnologias depende da calibração adequada do sistema de injeção, do projeto do motor e da qualidade do etanol utilizado.
Além disso, é necessário considerar as limitações e desafios associados, como a disponibilidade de infraestrutura de abastecimento de etanol e a necessidade de maior resistência dos materiais devido às características corrosivas do etanol em altas concentrações. Em suma, a combinação de injeção direta de combustível, motores turboalimentados e o uso de etanol como combustível pode proporcionar melhorias significativas em termos de desempenho, eficiência e redução de emissões.
No entanto, é necessário um desenvolvimento cuidadoso e consideração dos fatores mencionados para aproveitar todo o potencial dessa configuração. Atualmente, ainda é necessário realizar maiores estudos sobre desenvolvimento sustentável, preservação ambiental e degradação do meio ambiente. Além disso, também é desejável um estudo mais aprofundado e aprimorado sobre uso de combustíveis, suas características, possibilidades e aplicações. Para que assim, seja possível desenvolver combustíveis e automóveis com maior autonomia, menor gasto energético, mais desempenho e que polua cada vez menos o meio ambiente. As limitações deste estudo se basearam na baixa frequência de estudos sobre sistema de injeção direta e sua correlação com o uso do etanol, além disso, nem todos os estudos eram atualizados, alguns deles eram bem antigos.
6. Referências
AMARAL, L. V. Desempenho de formulações experimentais de gasolina em motor monocilíndrico de ignição por centelha com injeção direta. Belo Horizonte, MG: Universidade Federal de Minas Gerais, 2019; p. 1-103. Disponível em: https://repositorio.ufmg.br/bitstream/1843/RAOA-BEKNK2/1/lucimar_ven_ncio_amaral.pdf. Acesso em: 19 abr. 2023.
AMORIM , R. J. Análise do aumento da razão volumétrica de compressão de um motor flexível multicombustível visando melhoria de desempenho. Belo Horizonte, MG: Universidade Federal de Minas Gerais, 2005; p. 1-217. Disponível em: https://repositorio.ufmg.br/bitstream/1843/SBPS-7B6JSS/1/disserta__o___rog_rio_jorge_amo rim.pdf. Acesso em: 25 abr. 2023.
ASSOCIAÇÃO BRASILEIRA DE NORMAS TÉCNICAS. Veículos rodoviários- Código de ensaio de motores- Potência líquida efetiva. Brasil: Associação brasileira de normas técnicas, 1996; p. 1-26. Disponível em: https://www.normas.com.br/autorizar/visualizacaonbr/10181/identificar/visitante. Acesso em: 21 abr. 2023.
BAÊTA, J. G. C.; PONTOPPIDAN, M.; SILVA, T. R.V. Exploring the limits of a downsized ethanol direct injection spark ignited engine in different configurations in order to replace high-displacement gasoline engines. Belo Horizonte, MG: Universidade Federal de Minas Gerais, 2015; v. 105, p. 858–871. Disponível em: http://www.inee.org.br/down_loads/eficiencia/exploring_the_limits_of_downsizing.pdf. Acesso em: 24 abr. 2023.
BAETA, J. G. C. Metodologia experimental para a maximização do desempenho de um motor multicombustível turboalimentado sem prejuízo à eficiência energética global. Belo Horizonte, MG: Universidade Federal de Minas Gerais, 2006; p. 1-290. Disponível em: https://repositorio.ufmg.br/handle/1843/SBPS-757QWN. Acesso em: 20 abr. 2023.
BARROS, J. E. M.; VALLE, R. M.; BAETA, J. G. C. Conversion Methodology of an automotive engine into an aeronautical engine. Ouro Preto, MG: 18th International Congress of Mechanical Engineering, 2005; p. 1-7. Disponível em: https://www.abcm.org.br/anais/cobem/2005/PDF/COBEM2005-2076.pdf. Acesso em: 27 abr. 2023.
BRASIL. INSTITUTO NACIONAL DE METROLOGIA, QUALIDADE E TECNOLOGIA. Tabelas de Consumo/Eficiência Energética. Brasil: Instituto Nacional de metrologia, qualidade e tecnologia, 2016; p. 1-44. Disponível em: http://www.inmetro.gov.br/consumidor/pbe/veiculos_leves_2016.pdf. Acesso em: 26 abr. 2023
CARVALHO, A. S. Utilização do sistema de injeção direta de combustível pela indústria automobilística nos motores do ciclo Otto. Brasil: Revista Científica Multidisciplinar Núcleo do Conhecimento, 2018; Ed. 11, v. 1, p. 27-41. Disponível em: https://www.nucleodoconhecimento.com.br/engenharia-mecanica/combustivel. Acesso em: 18 abr. 2023.
FAGGI, R. Formação de mistura ar combustível em motores de ignição por faísca a quatro tempos. São Caetano do Sul, SP: Universitário do Instituto Mauá de Tecnologia, 2012; p. 1-60. Disponível em: https://maua.br/files/monografias/formacao-de-mistura-arcombustivel-em-motores-de-ignicao-por-faisca-a-quatro-tempos.pdf. Acesso em: 13 abr. 2023.
FILHO, F. A. R. Projeto, construção e caracterização do desempenho de um motor de combustão interna provido de um sistema de ignição por lança chamas de carga estratificada. Belo Horizonte, MG: Universidade Federal de Minas Gerais, 2014; p. 1-230. Disponível em: https://repositorio.ufmg.br/handle/1843/BUOS-9UQRBN. Acesso em: 19 abr. 2023.
HEYWOOD, J. B. Internal Combustion Engine Fundamentals. Estados Unidos: Library of Congress Cataloging-iP.Publication Data, 1988; p. 1-482. ISBN 0-07-028637-X. Disponível em: https://gctbooks.files.wordpress.com/2016/02/internal-combustion-engine-fundamentalsby-j-b-heywood.pdf. Acesso em: 28 abr. 2023.
INSTITUTO DE DESENVOLVIMENTO E APRENDIZAGEM. Aula 01 – Introdução ao curso. Brasil: Instituto de Desenvolvimento e Aprendizagem, 2018; p. 1-107. Disponível em: https://portalidea.com.br/cursos/bsico-de-injeo-eletrnica-apostila02.pdf. Acesso em: 14 abr. 2023.
MAGALHÃES, H. M.; GAUTO, R. G. N. d. Motores a combustão interna, downsizing e suas aplicações. Taubaté, SP: Universidade de Taubaté, 2017; p. 1-33. Disponível em: http://repositorio.unitau.br/jspui/bitstream/20.500.11874/5359/1/Hyran%20M.%20Magalhaes %20e%20Rafael%20Galvao%20N.%20de%20Gauto-1.pdf. Acesso em: 20 abr. 2023.
MARSYAELINA, A. et al. Analysis of Exhaust Gas Emission from Gasoline- and Dieselpowered Vehicles in Sleman Regency. Indonesia: American Journal of Mechanical Engineering, 2019; v. 7, n. 4, p. 195-200. Disponível em: http://www.sciepub.com/reference/309274. Acesso em: 27 abr. 2023.
OZDOR, N.; DULGER, M.; SHER, E. Cyclic Variability in Spark Ignition Engines A Literature Survey. Estados Unidos: SAE Technical Paper 940987, 1994; p. 1-41. Disponível em: https://www.sae.org/publications/technical-papers/content/940987/. Acesso em: 25 abr. 2023.
PEDROZO, V. B. Desenvolvimento de motor de alta performance a etanol para a competição fórmula SAE através de simulação computacional e validação experimental. Santa Maria, RS: Universidade Federal de Santa Maria, 2010; p. 1-127. Disponível em: https://formulaufsm.files.wordpress.com/2016/05/tcc-pedrozo.pdf. Acesso em: 25 abr. 2023.
PULKRABEK, W. W. Engineering Fundametals of the Internacional Combustion Engine. Estados Unidos: University of Wisconsin, 1997; p. 1-426. Disponível em: https://2k9meduettaxila.files.wordpress.com/2012/09/engineering-fundamentals-of-theinternal-combustion-engine-2k9meduettaxila-wordpress-com.pdf. Acesso em: 19 abr. 2023.
RODRIGUES, M. A. F. Projeto de um motor de combustão interna de ignição por centelha e injeção direta operando com etanol. Araçatuba, SP: Centro Universitário Toledo, 2015; p. 1-44. Disponível em: https://servicos.unitoledo.br/repositorio/bitstream/7574/484/3/TCC_Marcos %20Fernandes.pdf. Acesso em: 10 abr. 2023.
SANTOS, R. F. E. d. et al. Injeção direta de combustível em motores de ignição por centelha. São Carlos, SP: Universidade de São Paulo, 200; p. 1-7. Disponível em: https://www.abcm.org.br/anais/conem/2000/MC8824.pdf. Acesso em: 14 abr. 2023.
SILVA , T. R. V. D. Estudo de estratégias de controle dos processos internos de um motor de combustão interna de injeção direta de etanol turbo-alimentado para maximização da eficiência global. Belo Horizonte, MG: Universidade Federal de Minas Gerais, 2017; p. 1218. Disponível em: https://repositorio.ufmg.br/bitstream/1843/BUOS-ASFFAR/1/binder1.pdf. Acesso em: 11 abr. 2023.
TITOLO, A. The Variable Valve Timing System – Application on a V8 Engine. Estados Unidos: SAE Technical Paper 910009, 1991; p. 1-8. Disponível em: https://www.sae.org/publications/technical-papers/content/910009/. Acesso em: 21 abr. 2023.