REGISTRO DOI: 10.69849/revistaft/ch10202503102010
Claudinei Aparecido de Souza
Dario José Crispim Inácio
Davi de Araújo
Edmilson Peres dos Santos
Edson Ferreira de Oliveira
Guilherme Roveri Cardoso
Orientador: Prof. Wilson Meneguelo
RESUMO
A Padronização e Redução de Desperdícios Através do Gerenciamento do Fluxo de Materiais está sendo incorporado pelas organizações comerciais e industriais a partir da evolução tecnológica. É vista como um processo capaz de aumentar a eficiência organizacional através da redução dos custos operacionais, bem como agiliza os processos de movimentação das mercadorias em toda cadeia de abastecimento. Padronizar e reduzir desperdícios é um grande desafio das organizações, pois podem fazer a diferença para a empresa ser competitiva no mercado.
Palavras-chave: Padronização, redução, logística interna, fluxo de materiais, distribuição interna de materiais.
ABSTRACT
The Standardization and Waste Reduction Through Material Flow Management is being built by trade organizations and industry from technological advances. It is seen as a process that can increase organizational efficiency by reducing operating costs and streamlines processes for handling of goods throughout the supply chain. Standardize and reduce waste is a big challenge for organizations because they can make a difference to the company be competitive in the market.
Keywords: Standardization, reduction, internal logistics f low of materials, internal distribution of materials.
1. INTRODUÇÃO
Na década de 70, com a aplicação de técnicas como Just-in-time ( JIT), Planejamento das Necessidades de Materiais ( MRP), Sistema de Controle de Produção por Cartão (KANBAN), Sistema Flexível de Manufatura ( FMS), Controle de Qualidade Total (TQC) e outras, as indústrias começaram a atingir seu limite máximo de produtividade. Fazia-se necessário construir um sistema que escoasse toda a produção, no volume e velocidade exigidos pelo mercado, e que ao mesmo tempo adicionasse o menor custo possível. Para a empresa, a pontualidade e a rapidez na entrega passaram a ser tão importantes quanto à venda e a produção, e o gerenciamento logístico passa a ser vital para agregar valor ao produto.
No âmbito externo, o fluxo de materiais deve integrar as empresas fornecedoras de matérias-primas e insumos, o fabricante, o distribuidor, clientes e consumidores, com o objetivo de obter melhorias na relação tempo e custos.
Segundo Moura (2001), em algumas cadeias de suprimentos, o fluxo de informação movimenta-se no sentido contrário ao fluxo de materiais, principalmente nas empresas de produção pesada. Como resultado, raramente a demanda e a oferta coincidem, havendo necessidade de se acumular estoques ao longo da cadeia de suprimentos que atuam como “ pulmões”, protegendo falhas de suprimento e a não confiabilidade das previsões de venda.
Nesta situação, os custos de inventário com reflexos no custo do capital de giro corroem os lucros. Partindo desta constatação, é importante conhecer os modelos de gestão disponíveis para o gerenciamento logístico do fluxo interno de informações e materiais como forma de obter vantagem competitiva.
1.1 OBJETIVOS
- Eliminar o desperdício de matéria prima;
- Aumentar a eficiência de mão de obra;
- Eliminar o desperdício de movimentação;
- Organização do fluxo de matéria prima;
- Otimização do processo;
- Aumentar a produtividade.
1.2 PROCEDIMENTOS E MÉTODOS ADOTADOS NESTE TRABALHO
A proposta é encontrar a metodologia adequada para verificar a aplicação de conceitos para auxiliar na solução do problema apresentado. Esta metodologia deve ser tal, que os conceitos sejam utilizados para se obter um entendimento mais profundo do funcionamento de um sistema operacional de produção; o qual terá como base de gestão ferramentas de Lean.
1.3 ESTRUTURA DO TRABALHO
Este trabalho está esquematizado da seguinte forma:
O capítulo 2 a seguir apresenta a empresa objeto de estudo desde sua fundação até sua visão de qualidade e objetivos.
O terceiro capítulo apresenta o embasamento teórico dos métodos utilizados para atingir os objetivos deste trabalho na implantação do projeto.
No capítulo 4 temos o estudo de caso da empresa objeto de estudo onde foram implementadas as melhorias.
O quinto capítulo apresenta a conclusão deste trabalho e com base nos resultados obtidos com a implantação do projeto.
O capítulo 6 a apresenta a bibliografia utilizada para a elaboração fundamentação teórica.
2. A EMPRESA E OS PROCESSOS
The Timken Company é uma multinacional americana, líder mundial na produção de rolamentos de rolos cônicos e aços. Fundada em 1898 por Henry Timken, a empresa veio para o Brasil em 1938 e desde então construiu uma trajetória de sucesso em nosso país.
A Timken fabrica rolamentos e outros componentes de precisão em aço e está entre os 100 maiores fabricantes de autopeças do mundo. Com 26,5 mil funcionários, em 2006 a companhia teve faturamento global de US$ 4 bilhões e, após investir US$ 7, 3 milhões no Brasil, alcançou um faturamento de US$ 100 milhões.
História da The Timken Company
Por mais de 100 anos, a Timken tem focado na criação de valor para diversas indústrias e segmentos de mercado. Fornecemos uma variedade de soluções para o gerenciamento de atrito e transmissão de potência para aplicações que vão de aviões e automóveis a equipamentos de mineração e instrumentos médicos. Crescemos consideravelmente desde nossa fundação em 1899, mas a essência de nossos negócios é ainda resolver os problemas de nossos clientes, como era quando o fundador Henry Timken patenteou um desenho de rolamento de rolos cônicos que tornou a vida mais fácil para operadores de carroças de transporte de carga e para suas mulas.
O início
Henry Timken, um fabricante de carroças de St. Louis, reconheceu que as carroças de transporte de carga tinham muita dificuldade para fazer curvas fechadas. Para resolver o problema, ele aplicou um desenho de rolamento de rolos cônicos que podia trabalhar com cargas radiais (peso) e axiais (força lateral ao fazer curvas). Os clientes tiveram vários benefícios com esta invenção. Primeiro, a aplicação funcionava mais suavemente, reduzindo custos de reparo e substituição. Em alguns casos, os rolamentos melhoraram tanto o desempenho das carroças que menos mulas eram necessárias para puxá-las. Finalmente, melhor resistência às forças laterais ao fazer curvas significavam menos chance de perder uma carga de mercadorias. Sempre focado no benefício do cliente, Henry rapidamente percebeu que o rolamento de rolos cônicos poderia melhorar o desempenho de produtos da mesma forma em muitas outras aplicações. Ele e seus filhos, H.H. e William Timken, rapidamente fundaram a The Timken Roller Bearing and Axle Company e começaram a construir o negócio que chegou ao que é atualmente.
Visão e nossos valores
Os clientes são o centro de tudo o que fazemos e isso se reflete na visão e nos valores de nossa empresa. Enquanto nossa visão define nosso destino, nossos valores são nosso plano estratégico, guiando nossas ações para o benefício de todos aqueles que investem na Timken.
Ética e integridade
O fundador da empresa, Henry Timken, disse “Se você tem uma idéia que pensa estar certa, leve-a até o fim, mas, acima de tudo, não coloque o seu nome em algo que possa vir a envergonhá-lo”.
Qualidade
A qualidade é à base da nossa promessa de marca e a chave para nossa competitividade mundial. Os funcionários da Timken são treinados em processos de qualidade para assegurar que os clientes, onde quer que estejam, recebam produtos e serviços com excelente qualidade e consistência.
Inovação
O mundo gira em torno da habilidade de criar, transferir e controlar movimento. A Timken influencia o movimento em todos os principais setores por meio de soluções inovadoras que melhoram o desempenho dos equipamentos de nossos clientes, enquanto proporcionam benefícios para a sociedade.
3. FUNDAMENTAÇÃO TEÓRICA
3.1 GERENCIAMENTO DO FLUXO DE MATERIAIS
A atividade produtiva de uma fábrica depende da movimentação correta e eficaz de três principais fatores: homem, máquina e material.
Normalmente, a administração logística das empresas está organizada como mostra a figura 1 .
Para que haja um bom funcionamento da linha de produção, deve haver integração do plano de movimentação de material com todas as funções que geram movimentos, já que qualquer movimentação de material, não importando o ramo industrial, gera um fluxo de materiais.
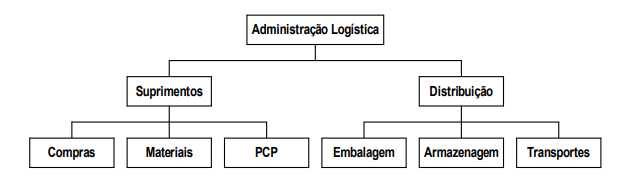
Figura 1 : Organização logística empresarial
Fonte: Representação gráfica idealizada pelos estudantes
O fluxo de materiais na movimentação interna de materiais possui uma seqüência de atividades que caracterizam a importância do gerenciamento dessa atividade. Apresentaremos essa seqüência no decorrer do texto.
3.2 ORGANIZAÇÃO DO SISTEMA DE MOVIMENTAÇÃO INTERNA DE MATERIAIS
A movimentação interna de materiais é responsável pela administração do fluxo de materiais, a partir do f luxo de informações recebido principalmente das áreas de produção, planejamento e controle da produção, assim como muitas vezes das áreas de compras e engenharia. Moura ( 1997 ), ao propor a equação de movimentação de materiais, material (o que?) + movimento (onde? e quando?), resulta no
método (como? quem?) para solucionar a questão, por que movimentar? ( figura 2), mostra que movimentar materiais, esteja eles em seu estado sólido, líquido ou gasoso, requer um ciclo completo de operações que necessariamente passam pela fonte de matérias-primas, pelo seu recebimento e estocagem, e pela sua movimentação entre as diversas fases de processamento até o produto acabado, administrando ainda a embalagem, armazenagem e distribuição.
Na movimentação interna de materiais, destacam-se:
- Recebimento
- Estocagem
- Distribuição interna dos Materiais
- Movimentação durante o processo
- Estocagem durante o processo
- Movimentação ao local de trabalho
- Movimentação interdepartamental
- Movimentação intradepartamental
- Movimentação interna da fábrica
- Movimentação relacionada com funções auxiliares
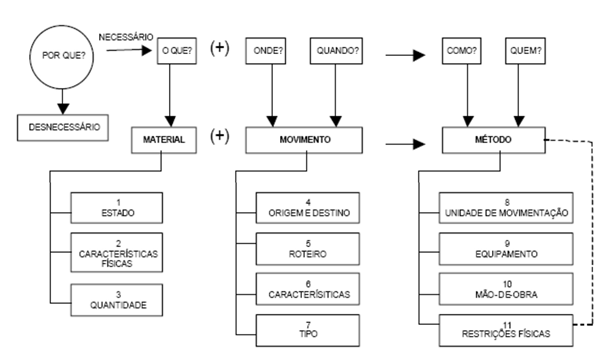
Figura 2 – A equação da movimentação interna de materiais
Fonte: Moura, 1997
- Embalagem (para consumo)
- Armazenagem de produtos acabados
- Embalagem (para transporte)
- Carregamento e expedição
- Movimentação entre plantas de um mesmo complexo industrial
Podemos classificar ainda a movimentação e o transporte de material de acordo com a atividade funcional a que se destina:
- Granel – Abrange os métodos e equipamentos de transportes usados desde o recebimento, estocagem e transporte interno de toda a espécie de materiais a granel, incluindo gases, líquidos e sólidos;
- Cargas Unitárias ou unitizadas – Cargas acondicionadas em um recipiente de paredes rígidas ou individuais ligadas entre si, formando uma única unidade para manipulação;
- Embalagem – Recipientes usados para o transporte de produtos no processo de produção ou de produtos acabados;
- Acondicionamento ou Armazenamento – Corresponde ao empilhamento ou colocação em prateleiras ou em suportes especiais, assim como a expedição de cargas de qualquer forma, em qualquer fase do processo de manufatura, desde o recebimento da matéria- prima até a expedição do produto;
- Vias de Transporte – Abrange o estudo do carregamento, desembarque e transferência interna de qualquer tipo de material por qualquer tipo de modal de transporte; e
- Análise de Dados – Nessa área estão contidos todos os aspectos analíticos da movimentação interna de materiais, tais como: levantamento de mapas de movimentação e manuseio, disposição física de equipamentos, organização, segurança, treinamento, manutenção, análise de custos e outras técnicas para o desenvolvimento de um sistema eficiente de movimentação de materiais.
Um sistema de movimentação de materiais em uma indústria tem que cumprir as seguintes finalidades básicas:
- Redução de custos. Melhor utilização de equipamentos, acondicionamento, racionalização de movimentação interna e armazenagem, permitem obter redução de custos de mão- de-obra, materiais e despesas gerais;
- Capacidade Produtiva. Sistema de movimentação eficiente permite aumento de produção, capacidade de armazenagem e melhor distribuição de armazenagem;
- Condições de Trabalho. Maior segurança, redução da fadiga e maior conforto pessoal são melhorias possíveis de serem acrescentadas no processo de produção pelos sistemas de movimentação de material; e
- Distribuição. Atividade que se inicia na recepção dos materiais e que se estende até a expedição do produto, permitindo melhoria na circulação, localização estratégica de almoxarifados e melhoria nos serviços ao usuário.
3.3 RECEBIMENTO
Qualquer que seja o tipo de produto gerado pelo processo industrial, o início da movimentação de materiais é o recebimento. Após a permissão para descarregar, o responsável pela entrega empilha todos os itens no recebimento e o material passa pela conferência que analisará a nota fiscal e o produto a ser recebido. Dependendo da origem e do tipo de produto, são necessárias análises qualitativas, por meio de amostragem. É responsabilidade do conferente garantir a entrada de um produto de qualidade para que sejam evitadas trocas e perda de tempo, pois produto parado gera prejuízo.
Na maioria das organizações o recebimento é uma atividade não valorizada, sendo, portanto, o portão de entrada da ineficiência ou baixa produtividade. Mesmo em modernas instalações, ainda se encontra o trabalho realizado no recebimento como lembrança dos tempos medievais. A descarga manual, falta de planejamento do fluxo e lentidão no processamento, atrasa os próximos passos do processo. No recebimento inicia- se também o processamento das informações. A ação física inicia- se com a recepção do veículo, e o sistema de informações deve responder a seguinte pergunta: a entrega pode ser aceita? A figura 4 mostra o diagrama de fluxo das atividades no recebimento:
Analisando o fluxo de materiais no recebimento, algumas considerações se fazem necessárias:
- Métodos de descarga devem ser padronizados para cada tipo de carga;
- Avaliação das cargas deve ser feita de acordo com suas características, tais como:
- tipo de embalagem das cargas (caixas de madeira, papelão, tambores, paletes)
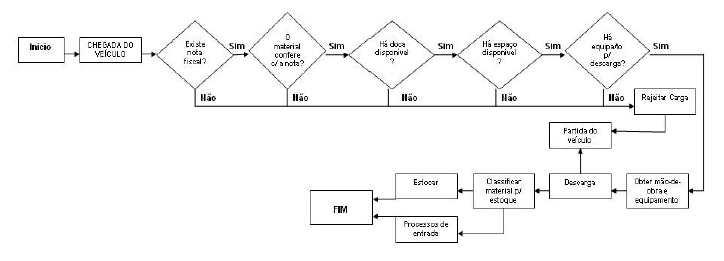
Figura 3 – Recebimento: diagrama de fluxo das atividades do recebimento
Fonte: Representação gráfica idealizada pelos estudantes
– quantidades de cada t ipo de carga recebida
– tamanho das embalagens
– peso das cargas/movimento
– peculiaridades de cada tipo de carga
– número de recebimento por período
– número de recebimento por tipo de veículo
– métodos de descarga, e
– tempo necessário para descarga
- Avaliação das atividades de abertura das caixas ou volumes para conferência qualitativa e quantitativa, permitindo o desenvolvimento de planos para reduzir essas atividades;
- Avaliação da documentação (recebida e emitida) durante o recebimento e o desenvolvimento de planos para reduzi-la;
- Mecanização das operações de descarga;
- Horários programados para recebimento de cargas;
e
- Planejamento para movimentação de cargas diretamente do ponto de recebimento para o ponto de estocagem
O recebimento inclui, portanto, todas as atividades envolvidas na recepção dos materiais, cujo objetivo principal para Moura (1997 ), geralmente envolve:
- Controle e programação das entregas;
- Obtenção e processamento de todas as informações para que a armazenagem possa identificar:
- Necessidade de estocagem especial
- Localização do estoque existente
- Considerações de estocagem FIFO (First In – First Out), primeiro a entrar, primeiro a sair.
- Análise de documentos para subsidiar planejamento;
- Programação e controle para manter a operação balanceada;
- Sinalização que permita facilitar a descarga e evitar demora;
e
- Coordenação do processo burocrático envolvido na inspeção de materiais com o trabalho físico de descarga.
3.3.1 As Funções do Recebimento
A rotina típica de recebimento pode ser descrita desta forma:
- Um funcionário do recebimento diz o horário específico da entrada da carga. Devem ser evitadas quaisquer chegadas sem aviso.
- Quando o veículo chegar, indicar ao motorista uma doca específica.
- Certificar-se de que o veículo esteja bem firme na doca, através do escoramento das rodas.
- Registrar e verificar o lacre do veículo na entrada, para ter certeza de que a carga não foi violada antes da chegada.
- Comprar o registro de recebimento com o aviso antecipado, com uma ordem de compra ou com alguma outra documentação.
- Registrar todas as exceções, inclusive excesso, falta ou danos.
- Fotografar quaisquer condições incomuns encontradas no recebimento.
- Fazer quaisquer verificações necessárias de controle de qualidade, sem demora.
- Definir um local de estocagem no armazém para a carga.
- Levar a carga da doca de recebimento até o local definido.
A verificação da contagem no recebimento é de importância critica. Existem mais roubos na área de recebimento do que na área de expedição, simplesmente porque é mais fácil perder o controle da contagem de quantidades no recebimento do que na expedição.
Aqui estão várias técnicas efetivas para minimizar as perdas no recebimento:
a) Pedir aos empregados do recebimento para trabalharem em duplas e verificarem um o trabalho do outro. Enfatizar o trabalho em equipe, em vez da competição.
b) Se as mercadorias tiverem de ser paletizadas, calcular o número de paletes destinadas para manter a carga inteira e passar esse número para o recebedor. O preenchimento de um número específico de paletes pode servir como uma verificação dupla contagem. Outra maneira de verificar duplamente a contagem é o uso de etiquetas ou adesivos, contados anteriormente, aplicando- se em caixa e preenchendo-os à medida que a mercadoria é recebida.
c) Providenciar um registro separado de recebimento, destinado a facilitar a contagem das marcas, em vez de tentar usar o espaço das margens no recibo de entrega ou no conhecimento de embarque.
d) Exigir uma verificação independente, baseada no recebimento feito às cegas; não dizer ao funcionário do recebimento qual a contagem esperada.
e) Sempre contar duas vezes antes de assinar uma vez.
3.3.2 ARMAZENAGEM
Na seqüência do fluxo de materiais, a armazenagem é a etapa seguinte ao recebimento, seja de matérias-primas, materiais em processo, componentes adquiridos de terceiros, seja de todos os insumos necessários à manufatura. Cada produto, após o recebimento, deve ter seu local apropriado para estocagem, seja em prateleiras, rotôndas, câmaras frias, estrados ou até mesmo acondicionados no solo. Em geral, as empresas seguem um padrão específico de armazenagem: os produtos que chegam primeiro devem ser os primeiros a sair (FIFO).
A armazenagem é uma importante função para atender com efetividade a Gestão da Cadeia de Suprimento. Sua importância reside em ser ela um sistema de abastecimento em relação ao fluxo logístico, que serve de base para a uniformidade e a continuidade deste, assegurando um adequado nível de serviço e agregando valor ao produto. Porém, por estarem trabalhando com níveis de estoque mais baixos, os clientes demandam menores tempos de resposta dos seus fornecedores, aumentando a pressão por agilidade nos armazéns, que passam a ter menor tempo entre o recebimento do pedido e sua expedição nas docas.
A figura 4 mostra as exigências que as operações são submetidas, bem como os impactos operacionais que estas exigências ocasionam:

Figura 4 – Exigências sobre as operações de armazenagem e seus impactos operacionais
Fonte: LACERDA ( 2001 )
A eficiência da estocagem depende fundamentalmente da escolha do almoxarifado correto, que deve estar relacionado diretamente com a natureza do material que irá ser movimentado e armazenado. A administração correta desse estoque intermediário proporciona uma melhora significativa na movimentação e aproveitamento da matéria- prima, diminui a rejeição de peças danificadas por batidas, impactos ou mesmo perda de material por manuseio incorreto, reduzindo assim o custo logístico interno da empresa.
Os custos indiretos estão ligados diretamente à Administração. Um sistema que reduza despesas na supervisão, facilitando o exame da parte burocrática dos processos e que ao mesmo tempo garanta um melhor controle da produção, com certeza seria a solução para a redução desses custos. Além disso, é economicamente viável, pois conseguiria reduzir significativamente as despesas de operação e aumentar a produção com um reflexo direto no valor do custo por unidade.
A empresa possui quatro razões para destinar parte de seu espaço físico à armazenagem: reduzir custos, tanto de transporte como de produção; coordenar a demanda e o suprimento; auxílio no processo produtivo; auxílio no processo de marketing.
Entretanto, a armazenagem não agrega valor ao produto e sim, custos, pois seu processo é caracterizado mais como um prestador de serviços do que uma função que efetivamente agregue valor ao produto. Ainda assim, a armazenagem ainda é necessária para a sobrevivência das organizações.
O conceito básico dado à logística de armazenagem pelos autores em geral seria: “ um processo de gestão de fluxos de materiais, no momento em que o mesmo assume velocidade zero, garantindo assim, uma maior qualidade de serviço ao cliente, bem como maximizando a produtividade operacional com o melhor aproveitamento dos recursos disponíveis (tempo, espaço, equipamentos, pessoas, etc.)”
O termo estoque é usado normalmente para caracterizar recursos que serão transformados, ou mantidos em operação, incluindo estoques de materiais na manufatura ou estoque de informações em um escritório (figura 5).
Normalmente há uma diferença de ritmo e/ou taxa entre o fornecimento e a demanda. Se o item fosse fornecido assim que fabricado, não haveria necessidade de haver um estoque. Para ocorrer uma redução significativa no mesmo, deve haver esforços para casar as taxas de fornecimento e demanda. Estes são os principais objetivos do sistema Just in Time, um dos pilares da manufatura enxuta.
O principal objetivo da manufatura enxuta é a utilização do estoque para agilizar o f luxo de produção, ao contrário do método de produção em massa idealizado por Ford e Sloan, que desconsidera a existência do mesmo para que não existam meios de se esconder a ineficiência na produção.
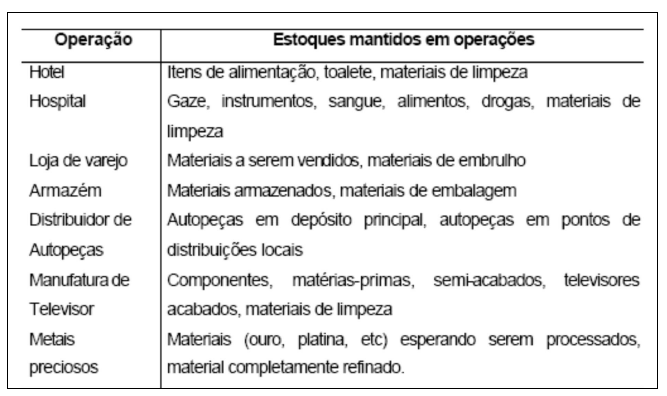
Figura 5 – Estoques mantidos em operaçõ es
Fonte: SLACK et. al., ( 1996 )
Muitas empresas que utilizam o conceito de produção em massa têm aumentado a freqüência de entregas de peças, porém, não estão produzindo em lotes menores, o que não significa uma melhoria na produção e sim apenas uma transferência de custos para o fornecedor.
Segundo análise do Lean Institute Brasil, a produção enxuta no Brasil enfrentará dificuldades devido ao alto grau de verticalização, às diferenças históricas entre as partes envolvidas, aos hábitos enraizados e à idade avançada das plantas que predominam nas indústrias brasileiras, essas serão por um logo tempo usuárias de estoque para balancear o fluxo de materiais no processo de produção. A existência de estoques torna a estocagem inevitável, pois os mesmos necessitam de depósitos para armazená-los.
Ao destinarem um espaço físico para estoques, as empresas podem optar por: possuir o depósito, alugar o espaço físico, alugar e estocar em trânsito. Cada uma das alternativas possui seu respectivo custo, risco e envolvimento em geral.
A armazenagem aumenta o valor do produto e seu custo. O consumidor não está interessado em pagar a mais por um produto apenas porque ele foi bem estocado ou mesmo porque seu estoque era de alta tecnologia, enfim, deve- se procurar aumentar a eficiência no abastecimento da produção, reduzindo assim os custos e o valor final do produto acabado.
A estocagem externa é uma boa alternativa para a redução de custos. A não ser pela desvantagem de problemas climáticos, ou custos com proteção que os mesmos possam gerar esse tipo de estoque não pode ser descartado. A eficiência da estocagem ao ar livre é determinada pela localização das mercadorias, pelas condições do solo e pelo equipamento utilizado.
Os principais exemplos de estocagem ao ar l ivre são:
- Estocagem de materiais soltos ou em pilhas;
- Empilhamento a granel;
- Silos e tanques;
- Estocagem de pós e grãos em silos
- Estocagem de líquidos em tanques;
- Depósitos para líquidos.
Uma das principais vantagens da estocagem externa é a ausência de altos custos de uma nova construção, pois será usado o espaço disponível ao ar livre da empresa, sendo apenas necessário uma proteção para eventos atmosféricos como chuva, ventos, geadas e etc.
Entretanto, a maioria dos materiais não suporta as adversidades do clima e necessitam ser estocados em ambientes fechados. Segundo Moura ( 1997 ), 60 % do investimento necessário para construir um armazém é gasto na construção do edifício e 40% nas instalações de estocagem e movimentação de materiais.
Quando se trata de estocar, o sistema ideal deve levar em conta as circunstâncias e as exigências de cada caso. O sistema ideal deve:
- Manter os estoques em um nível econômico, reduzindo o nível de capital investido;
- Otimizar o uso de espaço disponível, reduzindo o custo unitário de estocagem;
- Reduzir o período entre receber e expedir mercadorias, aumentando os lucros e proporcionando um melhor serviço ao usuário;
- Reduzir o custo da mão-de- obra, tornando-a mais eficiente;
- Reduzir os danos, as perdas e os roubos dos materiais;
- Planejar de forma a tornar os sistemas de estoque simples, é um instrumento de gestão a longo prazo.
A estocagem deve ser planejada envolvendo todos os detalhes: localização, layout, equipamentos e métodos de trabalho.
3.3.3 ARRANJO FÍSICO – LAYOUT
Arranjo físico ou Layout é a disposição de homens, máquinas e materiais que permite integrar o fluxo de materiais e a operação dos equipamentos de movimentação para que a armazenagem se processe dentro do padrão máximo de economia de rendimento.
O arranjo físico deve ter por objetivo:
- Assegurar a utilização máxima do espaço;
- Proporcionar movimentação de materiais da forma mais eficiente;
- Permitir uma estocagem mais econômica, minimizando as despesas de equipamento, espaço, danos de material, e a mão-de- obra do armazém;
- Proporcionar a máxima f lexibilidade do sistema que atenda as necessidades de mudança de estocagem e movimentação;
- Permitir a boa organização do armazém.
Existem muitas razões práticas que demonstram a importância do arranjo físico para a produção. A construção do mesmo de forma inadequada pode levar a padrões de fluxos excessivamente longos ou confusos, estoque excessivo de materiais, filas de usuários ao longo da operação, tempos de processamento desnecessariamente longos, operações e fluxos inflexíveis e/ ou de alto custo.
É muito importante saber o que se quer conseguir com um projeto ou arranjo físico. Primeiramente deve- se conhecer e compreender muito bem os objetivos estratégicos da produção e a participação do fluxo de materiais no processo.
O fluxo de material é o caminho percorrido pelos materiais desde a hora em que entram na empresa até o momento da saída. Um bom fluxo permite diminuir o custo de movimentação.
Para se obter um bom arranjo físico de um armazém, é necessário balancear três fatores:
a) Bom fluxo de material;
b) Custos de operação baixos para estocagem;
c) Correta e eficiente utilização do espaço de estocagem e do equipamento.
Para tanto, torna- se necessário considerar dois princípios básicos:
i. O retrocesso deve ser minimizado. Os itens devem ser movimentados sempre em direção a doca de expedição ( figura 6 , parte B).
ii. As atividades devem estar localizadas próximas, reduzindo a distância entre as operações (figura 7 , parte B).
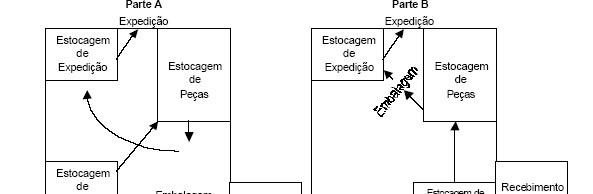
Figura 6 – Eliminação de retrocesso por mudança de layout
Fonte: MOURA ( 1997 )

Figura 7 – Localização de peças no estoque
Fonte: MOURA ( 1997 )
3.3.4 ABASTECIMENTO DA LINHA DE PRODUÇÃO
Normalmente, o processo de controle de materiais de uma empresa é definido pelo controle de produção adotado pela mesma, tendo ele duas possibilidades: o sistema empurrado (push) e o sistema puxado ( pull), denominado Kanban.
O Sistema empurrado (push) permite que as peças sejam estocadas em cada estágio de produção e são previstas considerando o tempo e o fluxo total para a finalização do processo no estágio final. O controle de produção e estoque é baseado no valor previsto.
Já o sistema puxado ( pull), tem como objetivo manter apenas pequenas quantidades de peças em cada fase, e sua reposição é ordenada pelo processo posterior na proporção que é consumida. A linha final de montagem sabe quantas peças serão necessárias e quando serão necessárias. Ela vai buscar as peças que necessita no processo anterior, desencadeando a retroalimentação do sistema. O sistema puxado (pull) é um dos principais pilares da filosofia JIT (Just in time).
O Sistema Just-in- time é uma forma disciplinada de melhorar a produtividade e a qualidade total pela eliminação das perdas, proporcionando apenas a produção das peças necessárias com qualidade, na quantidade, tempo e lugares certos, utilizando o mínimo de instalações, equipamentos, materiais e recursos humanos.
Na filosofia JIT, o estoque é o pior mal dentro de uma fábrica e é usado como uma proteção contra problemas conhecidos, como mudança de programas, escondendo muitas inadequações e custos no sistema.
A principal ferramenta para se estabelecer um sistema puxado de produção é o Kanban.
3.3.5 KANBAN
No final da 2ª guerra mundial o Japão estava destruído e precisava se reerguer. Por conta dos recursos escassos, esse desenvolvimento deveria acontecer sem nenhum tipo de desperdício. Surge então o conceito de Lean Manufacturing (Manufatura Enxuta) e Kanban.
Kanban, cujo significado é SÍMBOLO, PAINEL ou CARTÃO, é um sistema de controle da produção desenvolvido na Toyota Motor Company por seu ex-presidente, Mr. Taiichi Ohno. Dois pontos facilitaram a implementação do programa:
- A inexistência de recursos naturais, gerando uma atitude voltada ao combate ao desperdício;
- O elevado grau de conscientização de operário japonês com relação à importância da empresa onde trabalha e a retribuição, por parte desta, repartindo lucros obtidos com seus empregados.
O sistema KANBAN desenvolvido na Toyota começou a ser amplamente difundido no Japão a partir dos anos 70, após a segunda crise do petróleo. Foi quando as empresas japonesas verificaram que as fábricas da Toyota haviam superado as dificuldades sem sofrer grandes traumas. A f igura 8 ilustra duas técnicas para melhorar o desempenho do fluxo de informações na linha de produção, que apesar de serem bem diferentes uma da outra, ambas encontram oportunidades específicas de melhor desempenho.
Existem vários exemplos de interações entre ERPs e Kanban em um ambiente JIT, um deles mostraremos em seguida.
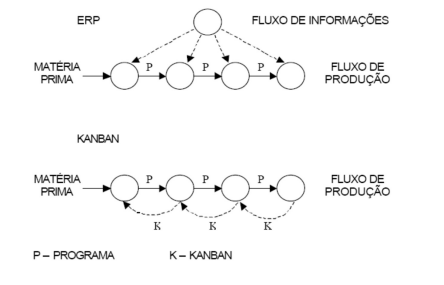
Figura 8 – Comparação entre ERP e KANBAN
Fonte: MOURA ( 1989 )
Na figura 9 a ordem de programa entregue pelo ERP é injetada apenas no lado de saída da célula de montagem final, isto é, na medida da necessidade do consumidor. Os cartões de Kanban circulam através do sistema alimentando o fluxo de informações necessárias, estágio por estágio, até o suprimento de matérias-primas, como ordens permanentes de trabalho.
Existe também a função do Kanban eletrônico, oferecida por sistemas informatizados. Nela é possível gerar automaticamente as informações do programa mestre e do planejamento de capacidade para controlar o ritmo de produção. O micro Kanban pode assumir a função do controle local do tráfego de material.
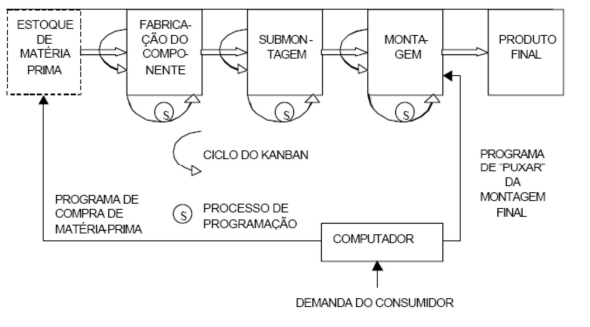
Figura 9 – Controle de pro dução com a interação entre ERP e KANBAN
Fonte: MOURA ( 1989 )
Eis aqui três propósitos do Kanban eletrônico:
- Descentralizar e ajustar o momento das necessidades recomendadas pelo ERP e controlar as necessidades de linha em tempo real;
- Emitir, movimentar e produzir componentes apenas quando necessários;
- Emitir relatório detalhado do controle de entrada e saída como suplemento de controle para o ERP.
3.3.6 SINAIS DE PUXADA E ROTAS DE ABASTECIMENTO – GESTÃO LEAN DA LOGÍSTICA INTERNA
As empresas no Brasil têm progredido na aplicação do fluxo contínuo de produção com resultados significativos na redução de estoques (Work in process), espaço e desperdícios internos às células. Porém, ainda não conseguem garantir que não ocorram interrupções no fluxo, porque as peças não estão disponíveis na hora certa ou na quantidade necessária. E ainda, muitas vezes definem estoques de peças elevados exatamente para livrar-se desse problema, com resultados freqüentemente desapontadores.
Esse é um dos motivos pelo qual o Brasil é um dos campeões mundiais em horas extras, forma encontrada para administrar o caos reinante em grande parte das operações industriais.
Um dos agravantes dessa situação é que na maioria das empresas o abastecimento de materiais acontece de maneira desordenada, não há um sinal que avise que a peça precisa ser reposta antes que ocorra uma interrupção do fluxo, (o sinal só ocorre quando acontece a parada da célula), há excesso de peças com pouco uso e falta de peças com uso mais freqüente, entre outras, ou seja, não há um sistema de entrega de materiais estabelecido.
De acordo com a filosofia Lean, os materiais devem fluir:
- Suavemente dentro, através e fora da produção, estabelecendo cadência;
- Sem faltas e sem excessos, garantindo estoques mínimos entre processos;
- Just in time, com rotas de abastecimento e freqüência de entregas estabelecidas.
Melhorando o fluxo interno de materiais:
- Os problemas tornam-se visíveis;
- Os estoques devem ser reduzidos;
- Libera- se espaço físico;
- A eficiência da mão de obra aumenta.
Para melhorarmos o sistema de movimentação de materiais precisamos entender tudo sobre a movimentação de cada peça:
- Como a peça é comprada?
- Como é recebida?
- Como é embalada?
- Onde é armazenada?
- Como é entregue ao seu ponto de uso?
Para isso, podemos utilizar uma ferramenta do Sistema Lean de Movimentação de Materiais denominada PPCP – Plano Para Cada Peça, que nada mais é do que uma base de dados criada para reunir e manter informações sobre todos os componentes comprados utilizados na manufatura. Veja abaixo um exemplo de PPCP:
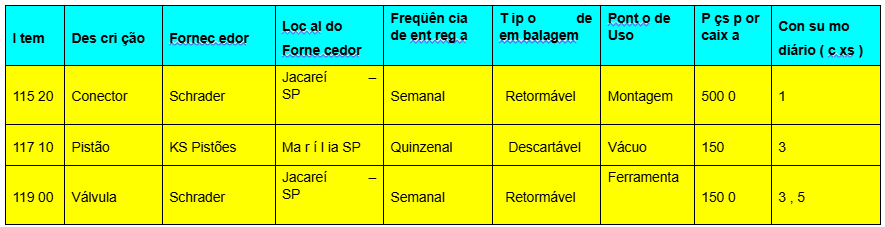
Figura 10 : Exemplo de PPCP
Fonte: HARRIS et. al. ( 2004 )
Com um PPCP bem definido, podemos desenvolver um estoque intermediário próximo ao ponto de uso, com as quantidades mínimas de consumo de cada item. Esse estoque é chamado de Supermercado, e sua função é manter os processos do fluxo constantemente abastecidos, independentemente de falhas logísticas, sazonalidades, etc., além de sinalizar ao processo fornecedor a necessidade de reposição. Funciona como um Kanban entre os processos e os fornecedores de insumos, subprodutos, matéria- prima, etc.
Para que o supermercado funcione corretamente, são necessários alguns procedimentos:
- Determinar localização específica para cada item;
- Utilizar identificações visuais;
- Identificar os níveis máximos e mínimos de abastecimento de cada item;
- Localizar o supermercado próximo ao local de consumo;
- Organizar o supermercado pelo sistema FIFO ( First In First Out).
3.3.6.1 Sinais de puxada
Para que as áreas de produção sinalizem o quê entregar e quando, é preciso implementar sinais de puxada que permitam a cada célula puxar do supermercado somente o material necessário. Essa sinalização pode ser feita através de kanban, sinais luminosos (andons), embalagens vazias, etc.
O importante é que o sinal seja a única autoridade para movimentar o material do supermercado à célula, pois é através dele que o departamento de Administração de Materiais, Planejamento de Produção ou Compras controla os níveis de estoque dentro da planta.
Mais adiante mostraremos em um estudo de caso um exemplo prático de sinal de puxada e supermercado.
3.3.6.2 Rotas de abastecimento
As rotas de abastecimento Lean são como o sistema cardiovascular em nosso corpo. Eles são as linhas da vida, entregando os nutrientes e retirando os resíduos para manter as células limpas com o que elas precisam, quando elas precisam. Também igualmente importante,
transportam os sinais das células para o organismo maior conforme as suas necessidades de mais materiais.
Uma função muito importante no sistema Lean de movimentação de materiais é a do Movimentador de Materiais. Ele é quem faz a ligação entre o supermercado e as células produtivas. Para que essa ligação seja bem executada, é preciso criar uma rotina de entrega para o movimentador que permita o contínuo abastecimento de todas as operações envolvidas, com tempo e freqüência estabelecidos. Chamamos essa rotina de Rota de Abastecimento.
A freqüência de entrega e o tempo total da rota variam conforme a necessidade de material em cada célula, mas o aconselhável é que a freqüência seja horária e o tempo de percurso não deve ser maior do que 33% do tempo total da rota.
A rota de abastecimento inicia e termina no supermercado. O movimentador retira do supermercado o material solicitado através do sinal de puxada de todas as células, sai do supermercado e pára em cada célula entregando o material e retirando o sinal de puxada da próxima hora, seguindo sempre o mesmo sentido. Volta ao supermercado, devolve sobras de material e separa o próximo material a ser entregue. A figura 11 mostra um exemplo de rota de entrega.
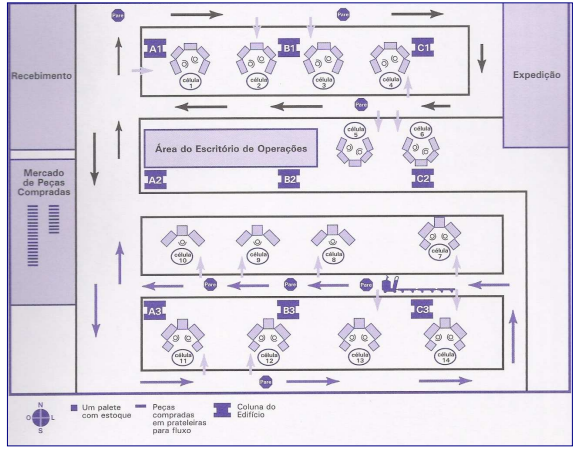
Figura 11 – Exemplo de rota de abastecimento
Fonte: HARRIS et. al. ( 2004 )
A filosofia Lean estabelece algumas regras para as rotas de entrega:
- Designar corredores de uma e duas mãos ao longo do percurso natural do f luxo na planta;
- A rota deve ser de uma hora;
- O sinal de puxada é a autorização para a movimentação do material e nenhum material deve ser movimentado sem ele;
- O operador da célula deve conhecer o nível mínimo de abastecimento para disparar o sinal de puxada;
- O tempo e a freqüência estabelecidos para a rota de entrega devem ser seguidos;
- As rotas devem fluir através da planta e voltar ao supermercado;
- Uma rota de uma hora deverá ter 57 minutos de eficiência de trabalho (95%);
- Sincronizar o horário de refeição e os intervalos do movimentador com aqueles que trabalham nas áreas atendidas por ele;
- Implementar trabalho padronizado rigoroso na rota de entrega para eliminar toda a movimentação desnecessária;
- Insistir que os tempos de rotas específicas e as freqüências sejam seguidos para que a rota de entrega não seja interrompida por qualquer motivo.
Um sistema Lean de movimentação de materiais cuidadosamente projetado e gerenciado é a maneira mais eficiente de transportar materiais e informações ao longo da planta por que:
- Reduz e controla os níveis de estoque;
- Atende a múltiplos clientes internos continuamente, além de minimizar o trabalho na movimentação de materiais;
- Facilita a entrega de peças, retirada de embalagens vazias e a movimentação da informação ocorre simultaneamente pelo mesmo movimentador de materiais;
- Libera espaço físico;
- Maximiza a eficiência de células em fluxo contínuo assegurando que as quantidades certas das peças certas estarão sempre à disposição.
Existem inúmeros benefícios adicionais de uma rota Lean de entrega de material. Isso inclui corredores e áreas limpas em volta das células e livres de estoques, materiais de embalagem e desperdício. Observe que a remoção de embalagens vazias e o abastecimento da célula produtiva são atividades agora realizadas pelo movimentador de materiais do supermercado e não pelos operadores de produção, onde essas atividades interrompem constantemente o fluxo de trabalho.
3.4 EMBALAGEM
A embalagem é um sistema integrado de materiais e equipamentos com que se procura levar os bens e produtos às mãos do consumidor final, utilizando-se dos canais de distribuição e incluindo métodos de uso e aplicação do produto.
O sistema de embalagem interage com todas as atividades ligadas a logística industrial e essa deve preencher algumas funções, tais como:
- Tecnológica: proteger por meios mecânicos, físicos e químicos as mercadorias;
- Mercadológica: exercer função de comunicação do conceito mercadológico;
- Econômica: manter o custo da embalagem controlado minuciosamente, pois em alguns casos, o custo da embalagem chega a ser maior que do que do próprio produto.
O sistema de embalagem e movimentação de materiais é um componente vital na logística, no sistema de fluxo de materiais. Quando se trata de embalagem e movimentação de materiais, surgem algumas preocupações que devem ser levadas em consideração:
- Como embalar o produto para melhor movimentação do mesmo, porém com baixo custo?
- Como embalar evitando danos ao produto e aplicar mais eficientemente os insumos destinados a ele?
- Como fazer com que a embalagem possa melhorar a integração com outras funções do sistema, otimizando assim, o sistema como um todo?
3.5 EXPEDIÇÃO
A última fase do ciclo de estocagem é o embarque dos produtos para o consumidor, ou a entrega do produto ao ponto onde será utilizado na fábrica.
O embarque é o último elo entre o fabricante e o consumidor. Todas as atividades que precedem a expedição são de pouco valor se a operação de expedição for ineficiente ou não econômica.
No planejamento das operações de expedição, é necessário que se considere os seguintes itens:
- Quantidade total a ser expedida.
- Peso total e ou volume a ser expedido.
- Número de pontos de embarque.
- Distâncias envolvidas.
- Meios de transporte.
- Datas de entrega.
- Documentação.
Após as mercadorias serem embaladas para a expedição, elas devem ser colocadas numa área de espera para o carregamento.
Isto consiste em marcar o piso com sinais, designando o cliente, a região geográfica, o transportador etc. As áreas podem ser usadas para cargas paletizadas.
Antes de ser retirado um item da área de expedição, este deve ser verificado da mesma maneira que as mercadorias que chegam. Isto é necessário para assegurar que o cliente receba o item correto, nas qualidades corretas e que a embalagem, o endereço etc. estejam corretos.
As operações de carregamento são influenciadas por fatores como: pessoal e equipamento disponíveis, equipamentos de transporte, característica do material a ser carregado etc.
Sempre que possível tais fatores devem ser conhecidos previamente, de modo que as operações de carregamento possam ser planejadas.
O carregamento pode também depender de diversos fatores, entre eles, os costumes dos carregadores locais, o relacionamento entre o carregador e o embarcador, a natureza das mercadorias etc.
O tipo de transporte a ser utilizado deve ser especificado pelo chefe de transporte, baseado no tipo de embarque disponível:
- Se é paletizado ou não;
- Se consiste em itens volumosos;
- Se é pesado e se tem peso concentrado;
- Se consiste em itens frágeis;
- Se são contamináveis, explosivos ou perigosos.
O tipo de transportes também pode ser determinado segundo outros fatores, como:
- Destino;
- Distância;
- Freqüência.
3.5.1 As Funções da Expedição
A maioria das funções ideais para a expedição é mais ou menos oposta às funções especificadas para o recebimento. Se um pedido destinado à expedição for retirado por um empregado, verificado e carregado por outro, a probabilidade da descoberta de erros aumenta muito. A insistência na manutenção de uma doca programada de expedição ajuda muito a evitar picos inesperados na carga de trabalho ou surpresas desagradáveis. A definição antecipada de uma contagem
específica das etiquetas de expedição é uma boa maneira de criar uma verificação dupla das quantidades na expedição.
A doca de expedição é um local excelente para a descoberta de erros cometidos pelos separadores de pedidos.
3.6 EQUIPAMENTOS DE MOVIMENTAÇÃO DE MATERIAIS
Movimentar materiais é uma tarefa que demanda grande esforço. A utilização de equipamentos adequados para cada tipo de material a ser transportado pode contribuir para uma melhor execução desta tarefa. Cada vez mais, novos equipamentos, mais modernos e sofisticados, são introduzidos no mercado, e a escolha do melhor equipamento depende de muitas variáveis, como o custo, o produto a ser manuseado, a necessidade ou não de mão de obra especializada, espaço disponível, entre outros.
Existe uma ampla variedade de equipamentos de movimentação de materiais de tamanhos, volumes e formas diversas. Os tipos mais comuns são:
I) Sistemas de transportadores continuos
Consiste na movimentação constante entre dois pontos predeterminados. São utilizados em mineração, indústrias, terminais de carga e descarga, terminais de recepção e expedição ou em armazéns.
São exemplos de sistemas de transportadores continuos:
- Esteiras transportadoras: São equipamentos de ampla aplicação, podem ser de correia, fita ou de tela metálica utilizadas geralmente para grandes quantidades de material. As fitas metálicas podem ser feitas de aço-carbono, aço inoxidável e aço revestido por borracha. Nas esteiras o ângulo máximo de inclinação é função das características do material (entre 20 e 35º). As esteiras transportadoras
- apresentam a desvantagem de possuir uma pequena flexibilidade na trajetória.
- Transportadores de roscas: São indicados para a movimentação de materiais pulverizados não corrosivos ou abrasivos. São normalmente utilizados em silos, moinhos, indústria farmacêutica, etc. O transporte é feito através da rotação do eixo longitudinal do equipamento.
- Transportadores magnéticos: utilizado para a movimentação de peças e recipientes de ferro e aço. Consiste em duas faixas de ferro magnetizadas por ímãs permanentes colocados na parte posterior de um transportador de fita, com um pólo em cada faixa, assim, o material ferroso é conduzido e atraído simultaneamente, podendo seguir em trajetórias verticais e horizontais, ser virado, freado, etc. Vantagens: é silencioso, requer pouco espaço e manutenção, trabalha embaixo d’água. Desvantagens: só transporta materiais ferrosos.
- Transportadores pneumáticos: utilizado para transporte de materiais granulados em silos, moinhos e portos. Constituem-se em um conjunto de tubulações e de um sistema motor que produz a corrente de ar. Vantagens: funcionam em qualquer tipo de trajeto, a vedação é completa, requer pouco espaço, baixos custos de manutenção. Desvantagens: somente utilizado para materiais de pequena granulométrica e não abrasivos.
- Transportadores de roletes livres: não há mecanismo de acionamento (somente a força da gravidade ou manual). É um sistema de transporte econômico, não há manutenção, permite o transporte de todos os materiais não a granel. A superfície de fundo do material deve ser dura e plana e no mínimo três roletes devem estar agindo simultaneamente sobre a carga.
- Transportadores de correntes: Evitam problemas de contaminação e permitem o aproveitamento do espaço aéreo. O investimento inicial e o nível de manutenção são baixos.
II) Sistemas de Manuseio para Áreas Restritas
São feitos para locais onde a área é elemento crítico: por isso são bastante utilizados em almoxarifados. A ponte rolante é o equipamento mais utilizado entre todos.
- Pontes rolantes: Viga suspensa sobre um vão livre, que roda sobre dois trilhos. São empregadas em fábricas ou depósitos que permitem o aproveitamento total da área útil (armazenamento de ferro para construção, chapas de aço e bobinas, recepção de carga de grandes proporções e peso). Vantagens: elevada durabilidade, movimentam cargas ultra pesadas, carregam e descarregam em qualquer ponto, posicionamento aéreo. Desvantagens: exige estruturas, investimento elevado, área de movimentação definida.
- Stacker Crane: Consiste numa torre apoiada sobre um trilho inferior e guiada por um trilho superior. Pode ser instalada em corredores com menos de 1 metro de largura e algumas torres atingem até 30m de altura. Exige alto investimento, mas ocasiona uma grande economia de espaço.
- Pórticos: São vigas elevadas e auto- sustentáveis sobre trilhos. Possuem sistema de elevação semelhante ao das pontes rolantes. Os pórticos são utilizados no armazenamento em locais descobertos. Vantagens: maior capacidade de carga que as pontes rolantes, não requerem estrutura. Desvantagens: menos seguro, interfere com o tráfego no piso, e é mais caro.
III) Sistemas de Manuseio entre Pontos sem Limites Fixos
É o mais versátil dos sistemas.
- Carrinhos: São os equipamentos mais simples. Consistem em plataformas com rodas e um timão direcional. Possuem vantagens como baixo custo, versatilidade, manutenção quase inexistente. Desvantagens: Capacidade de carga limitada, baixa velocidade e produção, exigem mão- de-obra.
- Paleteiras: Carrinhos com braços metálicos em forma de garfo e um pistão hidráulico para a elevação da carga ( pequena elevação). As paleteiras podem ser motorizadas ou não.
- Empilhadeiras: podem ser elétricas ou de combustão interna (verificar ventilação). São usadas quando o peso e as distâncias são maiores ( se comparadas com o carrinho) As mais comuns são as frontais de contrapeso. Vantagens: livre escolha do caminho, exige pouca largura dos corredores, segurança ao operário e à carga, diminui a mão-de-obra. Desvantagens: retornam quase sempre vazias, exige operador especializado, exige paletização de cargas pequenas.
As figuras abaixo i lustram alguns modelos de equipamentos de manuseio entre pontos sem limites fixos:
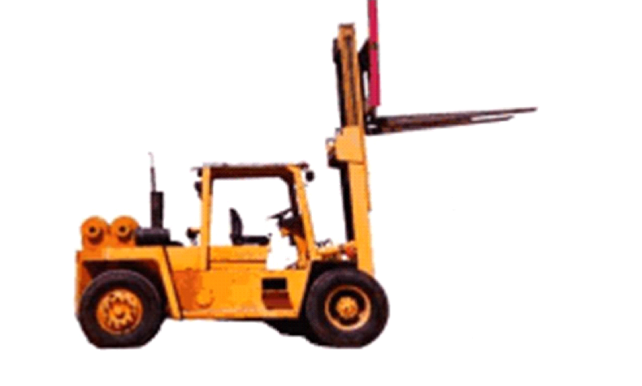
Figura 12 – Exemplo de empilhadeira
Fonte: Google Imagens
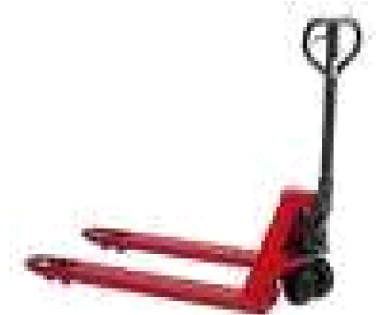
Figura 13 – Exemplo de Paleteira
Fonte: Google Imagens
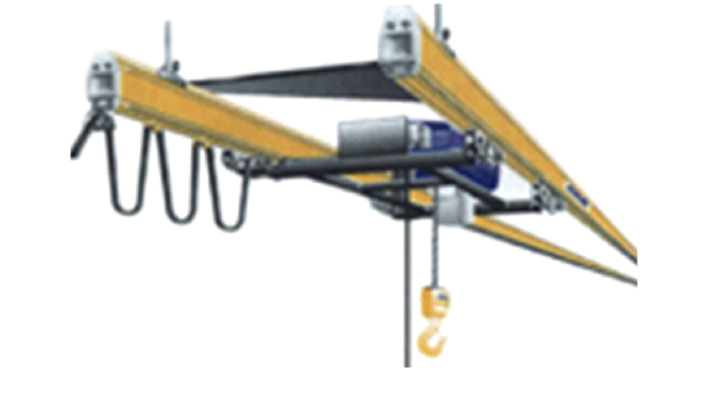
Figura 14 – Exemplo de Ponte Rolante
Fonte: Google Imagens
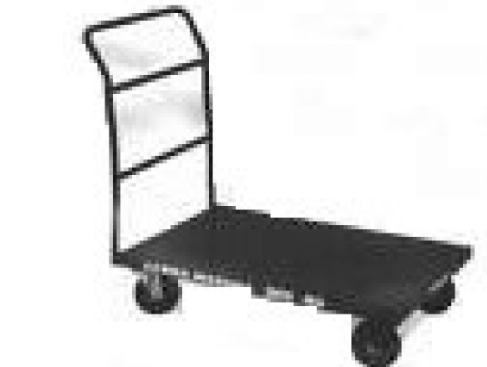
Figura 15 – Exemplo de Carrinho Manual
Fonte: Google Imagens
Os equipamentos ilustrados acima são os mais utilizados, porém existem outros também importantes, tais como:
- Guindastes: usados em pátios, construção pesada, portos e oficinas de manutenção. O veículo pode ser motorizado ou não. Opera cargas não paletizadas, versátil, alcança locais de difícil acesso, mas apresenta a desvantagem de exigir espaço e ser lento.
- Plataformas de Carga e Descarga: utilizadas no recebimento e na expedição de mercadorias, facilitando o trabalho. Geralmente são fixas.
- Mesas e Plataformas Hidráulicas: usadas basicamente na elevação da carga geralmente em conjugação com outro equipamento ou pessoa.
- AGV (Automatic Guided Vehicles): São utilizados desde 1950 podendo carregar até 100 toneladas. Os AGVs modernos são controlados por computador, possuindo microprocessadores e gerenciadores de sistema, que podem até emitir ordens de transporte e recolher ou descarregar cargas automaticamente. Existem diversos modelos, com os mais variados tipos de sensores e até por radiofreqüência. As desvantagens deste sistema são o custo e manutenção elevados.
- Dispositivos para Movimentação de Barris: utilização limitada, mas bastante útil para este tipo de material. Elimina a necessidade de paletização.
Existe uma grande variedade de equipamentos, deve-se avaliar o custo-benefício. O aumento da produtividade pode compensar gastos um pouco maiores. Em alguns casos, a escolha fica limitada ao tipo de material, espaço disponível ou o próprio custo. Não basta ter o equipamento certo, é preciso utilizá- lo de forma racional e otimizada.
3.7 CUSTOS LOGÍSTICOS E A MOVIMENTAÇÃO INTERNA DE MATERIAIS
Custo logístico é toda e qualquer despesa realizada em atividades de processamento, movimentação, armazenagem e transporte que compreende o fluxo de produtos ou informações. Podemos classificar as despesas logísticas em vários agrupamentos como movimentação, armazenagem, transporte, estoques, processamento de pedidos, embalagem, impostos e administrativos. Temos que considerar também os custos mais abrangentes do produtor, por exemplo:
- Custo da matéria- prima, produtos comerciais e subunidades.
- Custos de produção (mão-de- obra, estoque em processo).
- Custos de distribuição (fretes, preparações de pedidos, manutenções, estoque de produtos acabados e peças de reposição).
- Custos indiretos da produção (PCP, movimentação interna de materiais, etc.).
Entre estes e outros, os custos logísticos freqüentemente estão divididos ao longo de diversas funções, sendo assim difíceis de serem identificados. Muitos métodos de contabilidade existentes e mais usuais na indústria não fornecem informações apropriadas em relação a custos logísticos totais na cadeia produtiva. Bowersox e Closs (1996, pg 643) defendem que “o conceito básico de custo total é simples e complementa a noção de modelar a logística como um sistema integrado de desempenho”. O principal problema em operacionalizar o custo total é que as práticas contábeis tradicionais para classificar e apresentar despesas críticas não fornece uma métrica logística adequada. Para entender a demanda de se medir a logística, é necessário rever métodos da contabilidade tradicional em termos das exigências de análise e identificar os custos relevantes para sistemas logísticos integrados.
Os métodos de custeio tradicionais causam problemas particulares a medidas de desempenho e se esforçam em carregar, de forma arbitrária, custos indiretos a produtos ou clientes; acrescente ao fato a existência dos custos de ineficiências embutidos nas atividades operacionais internas da empresa onerando mais ainda a produção do bem e encarecendo o produto final; somando-se a isto, as empresas, no esforço para se manterem no mercado, freqüentemente adotam novas políticas administrativas visando melhorias de processos e redução de custos, porém até que se consiga adequar o processo novo da melhor forma à cultura da empresa, recursos podem estar sendo gastos de forma desnecessária merecendo uma atenção, intervenção se necessário, da controladoria no intuito de preservar o patrimônio da empresa, cabe à controladoria, por ser a única área com uma visão ampla e possuidora de instrumentos adequados à promoção da otimização do todo, a responsabilidade pelo cumprimento de uma missão muito especial. A missão da controladoria será: assegurar a otimização do resultado econômico da organização.
3.7.1 CUSTOS NA LOGÍSTICA INTERNA
Logística interna são atividades associadas ao recebimento, armazenamento e distribuição de insumos do produto, como manuseio de material, armazenagem, controle de estoque, programação de frotas, veículos e devolução para fornecedores.
A integração interna, ou seja, o gerenciamento integrado dos diversos componentes do sistema logístico, é uma condição necessária para que as empresas consigam atingir excelência operacional com baixo custo. A logística interna é diretamente responsável pela cadeia de valor da empresa quando procura otimizar os processos inerentes às atividades tais como a infra- estrutura do layout de distribuição interna da empresa e sistemas de informação, desenvolvimento de tecnologias de aquisição e atividades primárias de apoio, tais como manutenção de estoques mínimos, entrega dos produtos nos locais de utilização e outras atividades ligadas à produção para que o produto final saia no tempo correto com a qualidade ideal utilizando o mínimo de recursos possíveis, o que agregará valor ao produto. Mesmo quando ligadas a conceitos de planejamento divergentes como MRP/ERP e Lean Manufacturing a logística é uma atividade que pode se tornar o ponto crítico ou gargalo, já que diversos fatores, como um mau relacionamento com fornecedores e atrasos no recebimento podem afetar a produção de forma a desestabilizar a cadência produtiva e gerar atrasos de entregas, ociosidades e descompassos de mão- de-obra.
A produção por outro lado se prepara para lidar com tais gargalos administrando a flexibilidade de composto ( mix), como ressalta Slack ( 2002 , pg 75 ) “ A maioria das operações produz mais de um produto ou serviço. Além disso, a maioria delas não produz seus produtos ou serviços em volumes altos o suficiente para dedicar todas as partes de suas atividades exclusivamente a um produto ou serviço. Isso significa que a maioria das partes de qualquer operação terá que processar mais de um tipo de produto ou serviço e então precisará, às vezes, deixar uma atividade para dedicar-se a outra.”; porém esta flexibilidade gera custos. Custos estes que, ( onde todas as áreas têm planejamento estratégico, simulações, planejamento operacional, execução e controle, sendo obrigatória a existência de negociações, mediadas pela existência dos preços de transferências, entre elas), poderiam ser apontados e colocados como de responsabilidade da logística, que estaria consumindo um recurso da produção, o tempo de mão-de- obra disponível. Esta análise poderá servir de parâmetro para investimentos na área, já que caso os problemas não sejam resolvidos, continuarão a consumir os recursos.
Geralmente a falta de planejamento ou descontrole na logística se evidencia no momento em que a produção necessita do insumo e este não se encontra a disposição; ou seja, não há o mesmo em estoque. Três classes gerais de custos são importantes para determinar a política de estoques: custos de obtenção, custos de manutenção e custos de falta de estoque. Esses custos estão em conflito, ou em compensação, uns com os outros.
Essas políticas podem afetar a imagem da empresa no mercado e devem ser cuidadosamente estudadas. Uma empresa que opte em mudar suas operações para o sistema just- in- time por exemplo, deve fazer a transição de forma que esta não venha afetar o ciclo do pedido e o prazo de entrega final ao cliente, ou terá sua imagem afetada e seu conceito de competência, junto ao cliente, comprometida.
Dos custos acima citados, o mais comprometedor diz respeito à falta de estoques, que podem provocar comprometimento da lucratividade dos negócios da empresa.
Podem ser classificados em cinco tipos de custos; entre eles o “ custo das vendas perdidas e custo de pedidos em aberto”. Cada um pressupõe certas ações por parte do cliente, e, por causa de sua natureza intangível, são difíceis de serem medidos apuradamente. O custo das vendas perdidas ocorre quando o cliente, enfrentando uma situação de falta de estoque, escolhe retirar seu pedido. O custo é o lucro que seria obtido nesta venda particular e pode também incluir um custo adicional pelo efeito negativo que a falta de estoque pode ter em vendas futuras. O custo de pedidos em aberto ocorre quando um cliente esperará seu pedido ser preenchido, de modo que a venda não está perdida, apenas postergada. Os pedidos em aberto podem criar custos adicionais de serviços de escritório e de vendas para processar pedidos, e custos adicionais de transporte e de manuseio quando tais pedidos não são preenchidos através do canal normal de distribuição.
No caso do custo das vendas perdidas, pode- se acrescentar o custo do capital parado por produto em estoque, caso o mesmo não seja utilizado no momento planejado; o terceiro custo seria o custo de mão- de-obra ociosa quando a produção depende de certos insumos que não estão disponíveis no momento ideal para a sua utilização. Temos no valor do custo da mão de obra, entendida como o tempo do pessoal envolvido na operação dependente do insumo faltante; e, é claro, a necessidade de melhor tratamento do assunto.
Somando-se a estes, temos o custo da hora máquina, quando esta se torna necessária para a conclusão da operação; este custo envolve todo o período que a máquina se torna ociosa ou o tempo de setup desnecessário caso houvesse outra operação a ser desenvolvida. Nas atividades, os arranjos físicos devem estar na seqüência do roteiro de produção. Em algumas operações, há diferenças significativas no custo de mover materiais ou clientes entre diferentes centros de trabalho, por isso as distâncias entre os postos de trabalho devem ser as menores possíveis, para que os tempos de movimentação entre elas sejam os menores possíveis e se evite apontamentos de produto em trânsito. O orçamento de hora máquina deverá levar em conta o período para manutenção destas para seu perfeito funcionamento.
Por último podemos citar os custos do replanejamento operacional, pois se a falta ocasionou um atraso na produção e os prazos devem ser cumpridos, o atraso do insumo ocasiona sempre uma tensão muito grande principalmente entre as áreas da produção, prestação de serviços e comercial e requerem uma atenção especial para que o atraso não gere uma prorrogação em toda a carteira de clientes. O departamento comercial para manter seus índices de desempenho necessita dos produtos entregues nos prazos corretos, dependendo desta entrega para a manutenção da boa imagem e contatos para novas negociações com os clientes; os departamentos de produção e serviço necessitam do tempo apropriado para o processamento do produto com os níveis de qualidade satisfatórios e geralmente não detém recursos ( mão- de- obra e maquinário) disponíveis para focar o pedido em atraso e recuperar o tempo ocioso.
Entendemos então como custo do replanejamento, todo esforço do departamento empregado na recuperação do prazo de entrega final, obedecendo ao prazo do ciclo do pedido. Pode-se apontá- lo no período que é empregado em pedidos que já foram planejados uma vez. Temos mão-de- obra envolvida nos setores de planejamento, produção e expedição e, como estas estão sempre bem alocadas para que não haja perdas de processos normais, geralmente desencadeiam em horas extras, que devem ter os tratamentos específicos com adicionais e encargos relativos às áreas de trabalho.
3.7.2 GERENCIAMENTO DOS CUSTOS DA LOGÍSTICA INTERNA
A importância do gerenciamento dos custos de movimentação de materiais é justificada a partir da história do homem, quando necessitou do uso de ferramentas e máquinas para auxiliá- lo a realizar tarefas que estavam além da capacidade dos músculos humanos, como a construção das pirâmides, o transporte de água de poços e rios, a construção de barcos, o carregamento de suas cargas, forçando-o a desenvolver guindastes, talhas, carrinhos de mão e inventos similares. A partir da Revolução Industrial, o sistema industrial requereu contínuo desenvolvimento de equipamentos de movimentação para realizar tarefas para as quais os músculos humanos e dos animais eram insuficientes, tanto em capacidade como em velocidade. A evolução do sistema industrial não diminuiu a importância do custo da mão-de-obra e a percepção que a sua substituição por equipamentos de movimentação de materiais deixava de agregar custo ao produto, contribuindo para agregar valor.
A redução do custo de mão-de-obra é ainda a razão mais freqüentemente citada para justificar aperfeiçoamentos da movimentação de materiais. Todavia, a importância relativa do custo de mão-de- obra como componente do custo de fabricação está diminuindo. Em verdade, nem todos esses benefícios aparecem em todas as fases da movimentação de materiais. De modo oposto, sistemas de movimentação são freqüentemente justificados com base somente em uma ou algumas razões. Contudo, tanto o administrador como o engenheiro devem sempre procurar um ponto de vista bastante amplo, de forma a considerar as implicações globais de uma situação de movimentação de materiais. Os benefícios podem aparecer na forma de redução de capacidade ampliada e melhoria das condições de trabalho.
Os programas de redução de custos têm duas metas maiores: reduzir o custo da movimentação de materiais e reduzir os custos totais de produção através de melhores procedimentos de movimentação. O último conceito significa, algumas vezes, um aumento dos custos da movimentação de materiais para que seja obtida uma redução líquida nos custos totais de produção. Há outras formas pelas quais as reduções de custo podem ser realizadas através da melhoria da movimentação de materiais:
- Redução do trabalho de movimentação de materiais feito através de mão-de- obra direta;
- Redução da mão-de-obra indireta associada às atividades de movimentação física de materiais, tais como pessoal de expedição e recebimento, pessoal de controle de produção, pessoal de armazenagem e almoxarifado de ferramentas, inspetores, controle de qualidade, pessoal de reparos;
- Redução dos danos, perdas e extravios de materiais através de movimentação mais cuidadosa;
- Redução da burocracia e dos serviços de escritório associados, através de sistemas de movimentação que minimizem as necessidades de controle;
- Redução da quantidade de materiais no sistema através de um fluxo mais rápido e menos estocagem de materiais em processo; e
- Redução da quantidade de materiais auxiliares, tais como materiais de embalagem e outros acondicionadores.
As mercadorias geralmente não são produzidas no local onde são consumidas e requerem manuseio que incrementa o risco de dano ou perda do produto, adicionando custos. O correto gerenciamento do manuseio e armazenagem é essencial.
Produtos entregues com danos ou em volumes de difícil manuseio contribuem negativamente para a satisfação do cliente e, portanto, para que ele volte a comprar. Como a atividade de manuseio deve ser repetida muitas vezes, pequenas ineficiências em qualquer viagem podem acarretar grandes perdas quando aplicadas a muitos produtos por certo período de tempo.
Os métodos e equipamentos de movimentação interna passaram por grande evolução nos últimos tempos e talvez mais do que qualquer outra atividade da logística. A armazenagem e o manuseio de materiais deverão beneficiar- se da aplicação de novas tecnologias. A substituição de equipamentos deverá continuar à medida que a mão-de-obra fique mais cara. Sistemas informatizados são cada vez mais usados para controle de endereçamento e seleção de mercadorias. Sistemas de movimentação e armazenagem automatizados serão capazes de manusear grande variedade de produtos com maior flexibilidade.
Entretanto, os maiores ganhos virão da coordenação aperfeiçoada entre fornecedores e consumidores, além da aplicação generalizada dos métodos de manuseio modernos e de um gerenciamento eficiente e eficaz dos custos logísticos.
4. ESTUDO DE CASO: MELHORIA DA LOGÍSTICA INTERNA DO SETOR DE EMBALAGEM DO PRODUTO ACABADO NA TIMKEN DO BRASIL
4.1 O PROJETO DE MELHORIA
O setor de embalagem do produto acabado na empresa objeto de estudo é composto por nove células produtivas. A movimentação interna de materiais do setor é bastante prejudicada. Não há um estoque intermediário (supermercado) de materiais de embalagem e a distância do setor ao almoxarifado é de aproximadamente 250 metros. Sempre que qualquer célula precisa de qualquer material, o operador (a) tem que se deslocar do posto até o almoxarifado, o que a faz perder tempo de produção. Além disso, as sobras de material não tem um destino certo, já que o almoxarifado não aceita devoluções. Essas sobras são então deixadas em um espaço vago do setor. Como nada é identificado, essas sobras não serão consumidas, gerando desperdícios e ocupação desnecessária de espaço físico e movimentação.
Diante da situação exposta acima pode-se definir o seguinte problema: Como o Gerenciamento do Fluxo de Materiais pode auxiliar na redução dos desperdícios, na padronização e no aumento da produtividade?.
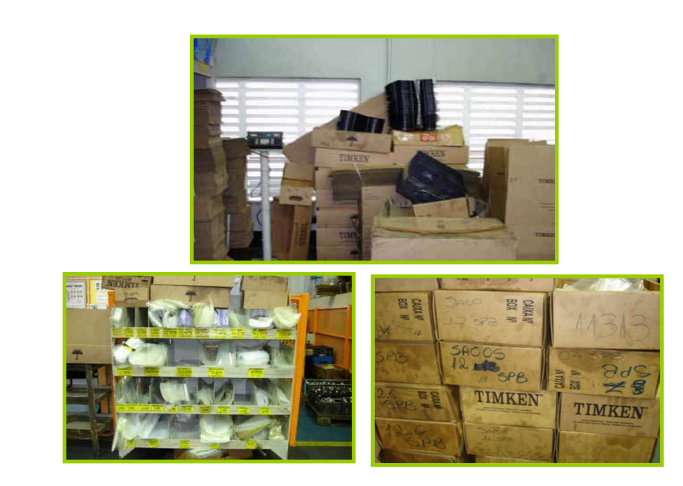
Figuras 16 – Estoque intermediário de embalagens
Fonte: Timken do Brasil
Durante uma semana, uma equipe multifuncional foi mobilizada para a melhoria da área. As ações tomadas foram:
a) Criação do supermercado de embalagens: todo material necessário para o processo de embalagem foi devidamente identificado e armazenado próximo às células. Veja fotos a seguir:

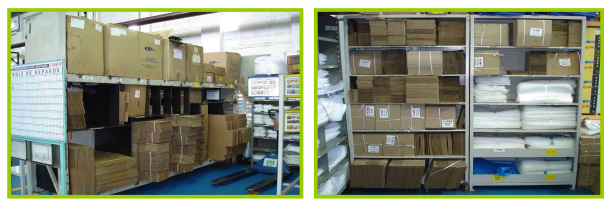
Figuras 17 – Supermercado de embalagem
Fonte: Timken do Brasil
b) Criação da função “ Movimentador de Materiais”: foi deslocado um colaborador específico para abastecer as células de embalagem, eliminando assim o desperdício de movimentação das embaladoras e as paradas de máquina por espera de material.
c) Implementação de Kanban para puxada de material do supermercado: foi implementado um sistema de pedido de material por kanban. Em cada setup a embaladora da célula preenche o kanban com
o próximo material a ser utilizado, e aciona o andon ( sinal luminoso) amarelo. Esse sinal simultaneamente é acionado no painel instalado no supermercado de embalagens. Veja as fotos a seguir:
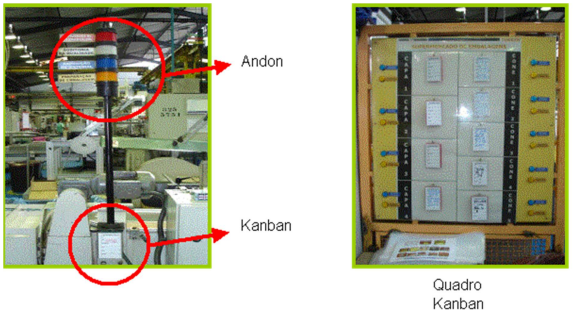
Figuras 18 – O sinal de puxada de material de embalagem
Fonte: Timken do Brasil
Ao ver o andon acionado, o movimentador de materiais vai até a célula, recolhe o kanban, deixa no quadro e leva o material solicitado. Quando a embaladora precisa de mais do mesmo material, ela aciona o sinal luminoso azul. O movimentador verifica no kanban o material que está sendo utilizado, abastece seu carrinho e entrega na célula solicitante.
O layout final do setor ficou assim definido:
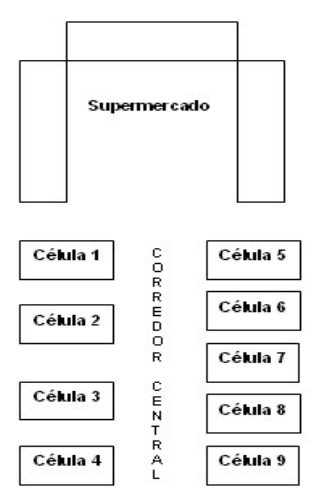
Figura 19 – Layout final do setor de embalagem do produto acabado
Fonte: Timken do Brasil
O projeto trouxe melhorias significativas para a empresa, como aumento da produtividade, redução dos problemas de qualidade por embalagem incorreta, etc. Isso é mais uma prova de que uma logística interna bem definida pode ser vista como forte estratégia competitiva.
5. CONSIDERAÇÕES FINAIS
Analisando o cenário industrial podemos observar que estamos em constantes mudanças na área de tecnologias de processamento e de gestão. Este avanço só é possível graças à globalização e também à nossa eficiência como usuários e fabricantes de equipamentos e produtos. Outro fator que merece atenção se refere a sistemas de gestão organizacional.
O Sistema de Produção Enxuta baseada no modelo de gestão é oportuno por possuir característica, a valorização do ser humano. A Manufatura Enxuta reúne ainda características favoráveis para o combate ao desperdício, o qual pode atingir até questões ecológicas, sociais e culturais, extrema preocupação com a satisfação do cliente, entrega dos pedidos no momento certo, na quantidade certa e com um preço atraente.
Com a implantação de um sistema de padronização e redução de desperdício através do gerenciamento do fluxo de materiais, implantando sistema kanban para controle do f luxo de insumos, criação de um sistema luminoso solicitando material pelo entregador, diminuindo o tempo de parada por falta de material, criando um supermercado para armazenamento de insumos necessários próximos aos postos de trabalho, alteração do layout do setor de embalagem melhorando o f luxo de materiais, implementação de um mapa de rota para entregador de material, aumentando a produtividade reduzindo perdas de matéria prima, e melhor aproveitamento de mão de obra.
Gerenciamento do fluxo de materiais nos sistemas de produção é hoje uma ferramenta indispensável para saúde financeira das empresas, pois visa aproveitar ao máximo recurso material e humano.
Devido a um mercado competitivo é necessária uma constante busca por melhorias de processos e produtos, buscando novas alternativas para reduzir desperdícios de insumos e mão de obra. O tema escolhido não teve o objetivo de esgotar o assunto e sim incentivar outros, engenheiros e gestores a buscar novas soluções e novos desafios que possam contribuir com as constantes necessidades de melhorias das empresas reduzindo tempo de seus processos, redução de matérias utilizadas e melhor utilização de mão de obra.
6. BIBLIOGRAFIA
BALLOU, Ronald H. Gerenciamento da cadeia de suprimentos: planejamento, organização e logística empresarial . Trad. Elias Pereira. 4 ª Edição, Porto Alegre: Editora Bookman, 2001 .
BERTAGLIA, Paulo Roberto: Logística e Gerenciamento da Cadeia de Abastecimento. São Paulo: Editora Saraiva, 2004.
FLEURY, Paulo Fernando; WANKE, Peter; FIGUEIREDO, Kleber Fossati ( org.). Logística empresarial: a perspectiva brasileira, 1 ª ed, São Paulo, Atlas, 2000. (Coleção COPPEAD de Administração)
HARRIS, Rick et. al. Fazendo Fluir os Materiais. São Paulo: Editora The Lean Enterprise Institute, 2004 .
MOURA, Reinaldo A. Sistemas e técnicas de movimentação e armazenagem de materiais. São Paulo: IMAM, 1997.
MOURA, Reinaldo A. Kanban – A simplicidade do controle de produção. São Paulo: IMAM, 1989.
SLACK, Nigel et. al. Administração da Produção. São Paulo: Editora Atlas, 2002.
MARTINS, Petrônio G.; LAUGENI, Fernando Peiero Administração da Produção e operações . Editora Saraiva, 2009.